Latest Articles
Corrosion protection for electronics systems in sewage treatment plants
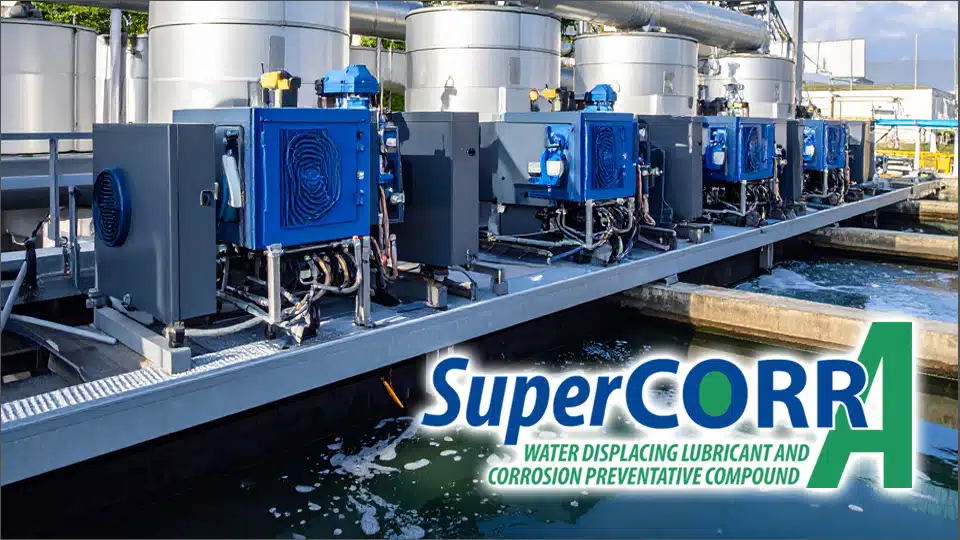
Corrosion protection for electronics systems in sewage treatment plants
Electrical control systems in sewage or water treatment plants operate in highly corrosive environments due to constant exposure to moisture, hydrogen sulfide (H2S), and other aggressive gases. Without adequate protection, components can fail prematurely, leading to downtime and safety risks.
Corrosion is an insidious and costly problem that causes just about every metal and metal alloy to fail over time. Metals in electrical and electronic control systems, components, connectors, and switches are of most concern. To combat this, engineers are increasingly turning to specialized corrosion inhibitors and protective coatings.
These solutions form a barrier against corrosive agents while allowing electrical systems to function reliably. Enclosures rated for harsh environments, combined with regular maintenance and smart material choices, further enhance system longevity. Implementing effective corrosion protection measures will safeguard operations and extend the lifespan of vital control systems in water treatment infrastructure
With proper corrosion protection, satellite components are less likely to deteriorate, lose functionality or break off, thereby reducing the risk of creating additional space debris and supporting sustainability in orbit. Corrosion-resistant materials and protective coatings like Super CORR A help protect metal and electronic equipment against corrosion and help to minimize the risk of degradation, lowering the frequency and cost of maintenance. Corrosion protection is fundamental to space industry operations, preserving both the physical integrity of the space-based structures and the success of the missions they enable. This is especially vital as the industry moves toward more ambitious projects.
Specialist corrosion protection for electronics in moist environments
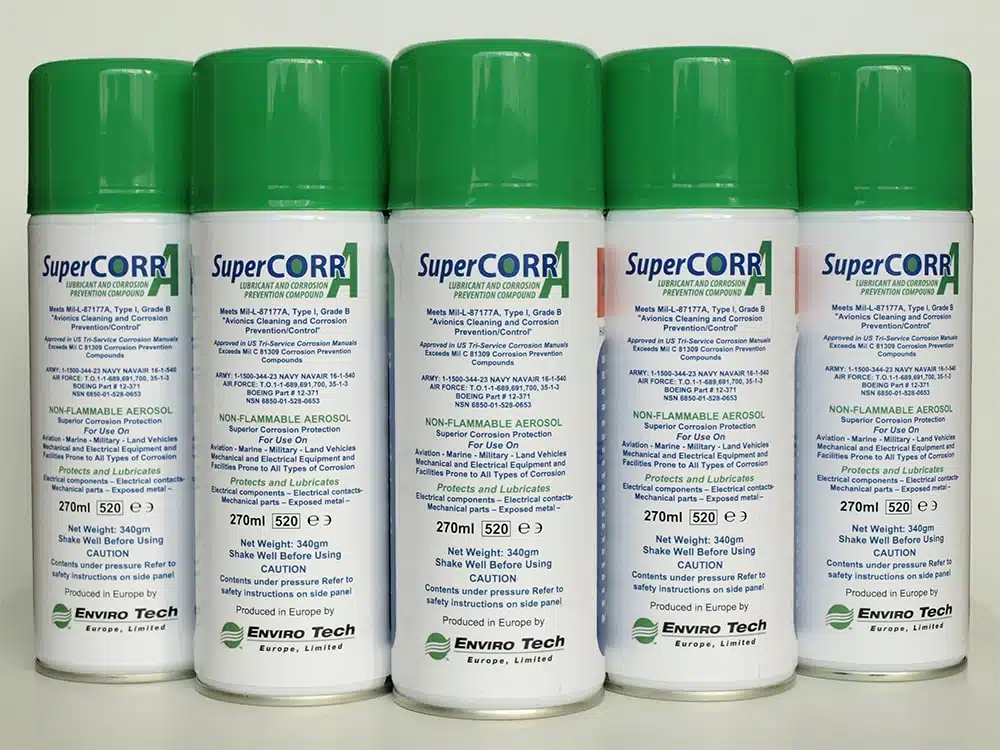
EnviroTech Europe produce and supply around the world advanced corrosion protection products, based on approved synthetic materials, to provide quality solutions to a diverse range of lubrication and corrosion problems.
Super CORR A is a “self-healing” ultra-thin film water displacing lubricant with long-lasting, anti-corrosion inhibitors providing a superior lubrication coefficient and protection against moisture, wear, general and fretting corrosion, static electricity, corona, and other electro migration problems. The non-flammable film is only 7 microns (0.007mm) in thickness, will not harden or crack, is not a wax or oil-based product and is formulated without sulphates, chlorides or halogens.
Super CORR A has a proven performance record in protecting electrical components, systems, connectors and electronics. The coating will also prevent the ingress of moisture and other contaminants onto the connector surfaces.
Removal of surface contamination from the metallic contact surfaces on switches and circuit breakers is essential to ensure fault free operation. An inert compound that neither reduces nor increases the electrical conductivity, Super CORR A ’s unique formulation lifts and removes dust and soils from the metal contact surfaces. It also provides long term protection from corrosion and electrical arcing that can lead to shorts and subsequent circuit failures. The aerosol spray is supplied with a flexible tube applicator which allows the protective coating to be applied accurately even in difficult to get to places.
EFFICIENT AND ECONOMICAL
- Extremely long-lasting, specially formulated and proprietary anti-corrosive inhibitor.
- Eliminates premature failure of components created by moisture, general or fretting corrosion.
- Prevents deterioration and contamination on all surfaces of electronic and electrical equipment and mechanical close tolerance moving components.
- Reliability increased, maintenance intervals increased and costs reduced, manufacturers save costly warranty service calls or product re-call.
- Non-flammable.
FURTHER INFORMATION
Please visit our website https://www.envirotech-europe.com/supercorr-a for information about other uses and applications for Super CORR A.
Visit www.envirotech-europe.com/applications-and-case-studies for information about uses and applications for all EnviroTech Europe products.
For more advice, please telephone us on +44 (0) 20 8281 6370 or use our website contact form.
All products are supplied and supported by EnviroTech Europe Ltd. Manufactured in the United Kingdom and available on short delivery times through our dedicated team of distributors worldwide.
Share this page:
PFAS-Free Precision Solvent Cleaner for Electronics
Next-generation PFAS-Free vapour degreasing solvent cleaner for electronics and electrical components
Evolving legislation by governments worldwide has resulted in the need for new and original formulations to be offered for use in solvent cleaning and vapour degreasing processes. Companies must continue to comply with legislation for protection of the environment and safety of operators who may be exposed to harmful substances such as PFAS chemicals. This has led to new formulations being developed for solvent cleaners. In applications where formulated blends of halogenated solvents have been used very effectively in the past, these are now required by changes in legislation to be phased out of use.
EnviroTech Europe have been supplying vapour degreasing solvent formulations for over 20 years, constantly responding to increasingly stringent regulatory requirements for environmental and safety laws and the need for improved cleaning standards. Our staff and distributors are trained to work with equipment suppliers to advise on the use of vapour degreasing solvents for the most satisfactory outcome.
EnviroTech Europe have developed a new solvent cleaning formulation based on recent research, a replacement for the “old” technology, which has been found to perform just as effectively without the negative environmental, health and safety issues.
High performance precision cleaning solvent with Zero Ozone Depletion Potential (ODP) and very low Global Warming Potential (GWP)
ProSolv 5408e has been developed to provide superior critical cleaning performance for manufacturers of electronic and electrical components. High Solvency (KB Value 98) for removal of organic residues, compatible with organic and synthetic oils and most plastics and metals.
ProSolv 5408e is a high-performance solvent cleaner used for sustainable and future proof vapour degreasing. It has a GWP of less than 1, with a 100 year Integrated Time Horizon (ITH). Soft on the environment and safe for users, it offers improved cleaning at lower costs.
ProSolv 5408e ticks all the boxes and is the perfect profile for a modern vapour degreasing solvent. Exceptionally low surface tension to penetrate micron sized holes and close contact surfaces. Sustainable and secure for the future. Non-carcinogenic, low boiling point, economical with energy with low solvent losses, faster production, reduced costs, easy handling.
ProSolv 5408e is compatible with most solvent cleaning systems including one-tank or multi-tank immersion and vapour degreasing equipment, using ultrasonics or flush cleaning. An excellent choice for removal of a wide range of organic soils by vapour degreaser, ultrasonic cavitation, dip tank, flushing. Energy-efficient, fast processing, low solvent loss, and easy handling, reducing both environmental impact and operating costs.
FEATURES AND BENEFITS
- PFAS Exempt
- GWP of less than 1
- Non-hazardous for transportation.
- Non-flammable (No Flash Point).
- Not classified as a carcinogen.
- RoHS compliant.
- Fast precision cleaning with short cycle times, fast drying.
- Stable with no additives, no testing required.
- Mid-range boiling point (46°C).
- High Solvency (KB Value 98) for a variety of contaminants.
- Compatible with a broad range of substrates.
FURTHER INFORMATION
Please visit our website https://www.envirotech-europe.com/prosolv5408e for information about other uses and applications for ProSolv®5408e.
Visit www.envirotech-europe.com/applications-and-case-studies for information about uses and applications for all EnviroTech Europe products.
For more advice, please telephone us on +44 (0) 20 8281 6370 or use our website contact form. All products are supplied and supported by EnviroTech Europe Ltd. Manufactured in the United Kingdom and available on short delivery times through our dedicated team of distributors worldwide.
Share this page:
Next-generation, PFAS-Free vapour degreasing solvents
Next-generation, PFAS-Free vapour degreasing solvents for modern industry
ProSolv®5408e is a next-generation, PFAS-free solvent that offers zero Ozone Depletion Potential (ODP) and low Global Warming Potential (GWP below 1), future-proofing your cleaning applications. Effectively removes organic residues and oils and is compatible with most plastics and metals. Exceptionally low surface tension and strong solvency allows it to reach tight spaces, blind holes and micron-sized holes.
ProSolv®5408e is compatible with most solvent cleaning systems including one-tank or multi-tank immersion and vapour degreasing equipment, using ultrasonics or flush cleaning. An excellent choice for removal of a wide range of organic soils by vapour degreaser, ultrasonic cavitation, dip tank, flushing. Energy-efficient, fast processing, low solvent loss, and easy handling, reducing both environmental impact and operating costs.
THE SOLVENT OF CHOICE FOR HIGH PERFORMANCE CRITICAL CLEANING
ProSolv®5408e has a unique range of characteristics which make it the vapour degreasing solvent of choice for critical cleaning applications in the following industries:
- Avionics and Aerospace
- Electronics and Electrical
- Environmental
- General Cleaning
- Industrial and Manufacturing
- Marine and Maritime
- Mechanical Engineering
- Medical Device Manufacturing
- Military
- Motorsport
- Oxygen Cleaning
- Precision Optics
- Power Generation
- Railways and Automotive
FEATURES AND BENEFITS
- PFAS Exempt
- GWP of less than 1
- Non-hazardous for transportation.
- Non-flammable (No Flash Point).
- Not classified as a carcinogen.
- RoHS compliant.
- Fast precision cleaning with short cycle times, fast drying.
- Stable with no additives, no testing required.
- Mid-range boiling point (46°C).
- High Solvency (KB Value 98) for a variety of contaminants.
- Compatible with a broad range of substrates.
FURTHER INFORMATION
Please visit our website https://www.envirotech-europe.com/prosolv5408e for information about other uses and applications for ProSolv®5408e.
Visit www.envirotech-europe.com/applications-and-case-studies for information about uses and applications for all EnviroTech Europe products.
For more advice, please telephone us on +44 (0) 20 8281 6370 or use our website contact form. All products are supplied and supported by EnviroTech Europe Ltd. Manufactured in the United Kingdom and available on short delivery times through our dedicated team of distributors worldwide.
Share this page:
Related Posts
Latest News
Corrosion protection for electronics systems in sewage treatment plants
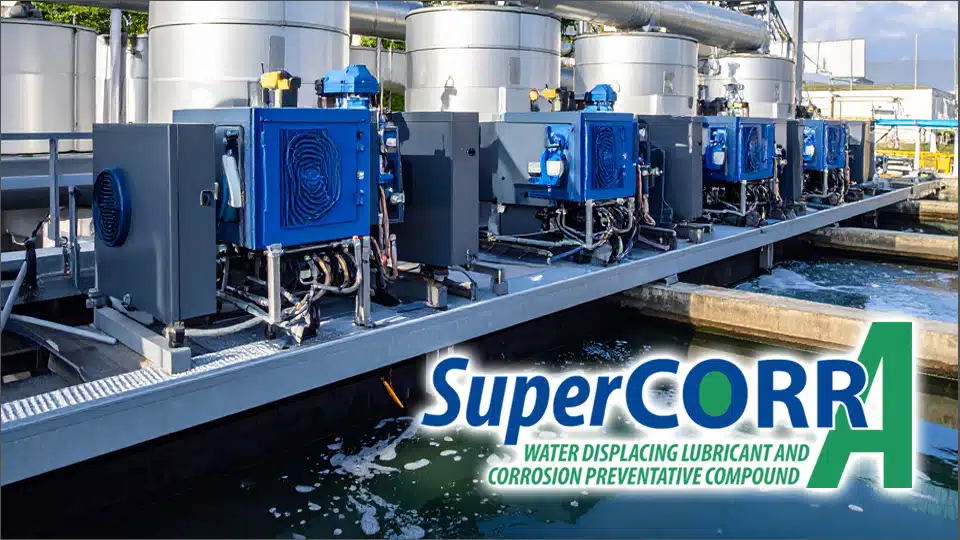
Corrosion protection for electronics systems in sewage treatment plants
Electrical control systems in sewage or water treatment plants operate in highly corrosive environments due to constant exposure to moisture, hydrogen sulfide (H2S), and other aggressive gases. Without adequate protection, components can fail prematurely, leading to downtime and safety risks.
Corrosion is an insidious and costly problem that causes just about every metal and metal alloy to fail over time. Metals in electrical and electronic control systems, components, connectors, and switches are of most concern. To combat this, engineers are increasingly turning to specialized corrosion inhibitors and protective coatings.
These solutions form a barrier against corrosive agents while allowing electrical systems to function reliably. Enclosures rated for harsh environments, combined with regular maintenance and smart material choices, further enhance system longevity. Implementing effective corrosion protection measures will safeguard operations and extend the lifespan of vital control systems in water treatment infrastructure
With proper corrosion protection, satellite components are less likely to deteriorate, lose functionality or break off, thereby reducing the risk of creating additional space debris and supporting sustainability in orbit. Corrosion-resistant materials and protective coatings like Super CORR A help protect metal and electronic equipment against corrosion and help to minimize the risk of degradation, lowering the frequency and cost of maintenance. Corrosion protection is fundamental to space industry operations, preserving both the physical integrity of the space-based structures and the success of the missions they enable. This is especially vital as the industry moves toward more ambitious projects.
Specialist corrosion protection for electronics in moist environments
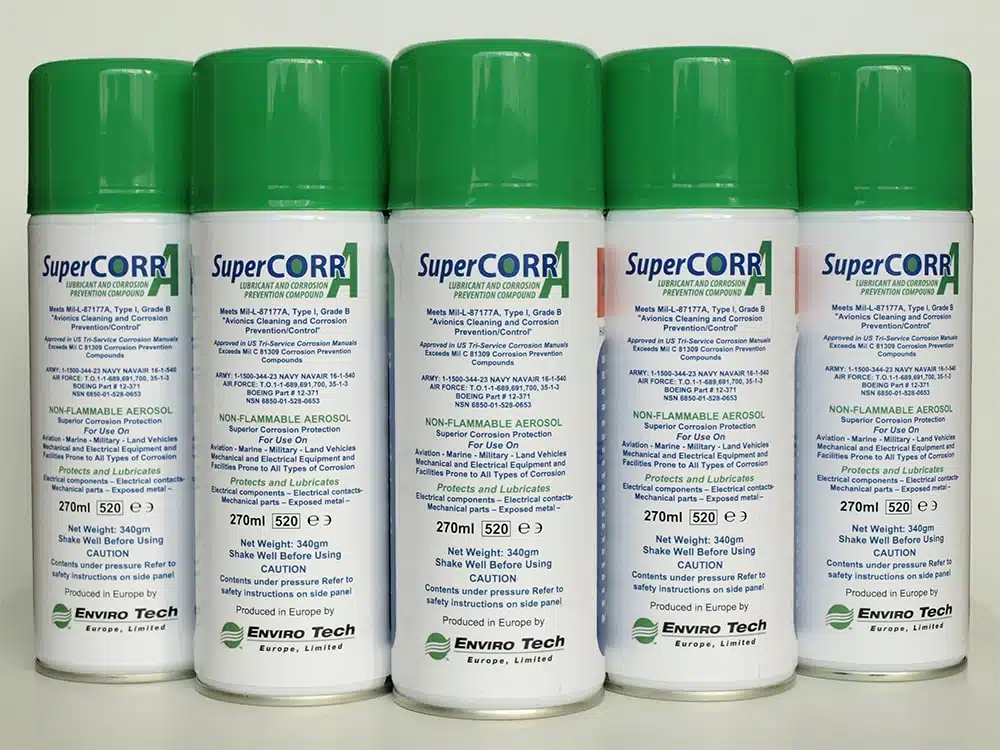
EnviroTech Europe produce and supply around the world advanced corrosion protection products, based on approved synthetic materials, to provide quality solutions to a diverse range of lubrication and corrosion problems.
Super CORR A is a “self-healing” ultra-thin film water displacing lubricant with long-lasting, anti-corrosion inhibitors providing a superior lubrication coefficient and protection against moisture, wear, general and fretting corrosion, static electricity, corona, and other electro migration problems. The non-flammable film is only 7 microns (0.007mm) in thickness, will not harden or crack, is not a wax or oil-based product and is formulated without sulphates, chlorides or halogens.
Super CORR A has a proven performance record in protecting electrical components, systems, connectors and electronics. The coating will also prevent the ingress of moisture and other contaminants onto the connector surfaces.
Removal of surface contamination from the metallic contact surfaces on switches and circuit breakers is essential to ensure fault free operation. An inert compound that neither reduces nor increases the electrical conductivity, Super CORR A ’s unique formulation lifts and removes dust and soils from the metal contact surfaces. It also provides long term protection from corrosion and electrical arcing that can lead to shorts and subsequent circuit failures. The aerosol spray is supplied with a flexible tube applicator which allows the protective coating to be applied accurately even in difficult to get to places.
EFFICIENT AND ECONOMICAL
- Extremely long-lasting, specially formulated and proprietary anti-corrosive inhibitor.
- Eliminates premature failure of components created by moisture, general or fretting corrosion.
- Prevents deterioration and contamination on all surfaces of electronic and electrical equipment and mechanical close tolerance moving components.
- Reliability increased, maintenance intervals increased and costs reduced, manufacturers save costly warranty service calls or product re-call.
- Non-flammable.
FURTHER INFORMATION
Please visit our website https://www.envirotech-europe.com/supercorr-a for information about other uses and applications for Super CORR A.
Visit www.envirotech-europe.com/applications-and-case-studies for information about uses and applications for all EnviroTech Europe products.
For more advice, please telephone us on +44 (0) 20 8281 6370 or use our website contact form.
All products are supplied and supported by EnviroTech Europe Ltd. Manufactured in the United Kingdom and available on short delivery times through our dedicated team of distributors worldwide.
Share this page:
PFAS-Free Precision Solvent Cleaner for Electronics
Next-generation PFAS-Free vapour degreasing solvent cleaner for electronics and electrical components
Evolving legislation by governments worldwide has resulted in the need for new and original formulations to be offered for use in solvent cleaning and vapour degreasing processes. Companies must continue to comply with legislation for protection of the environment and safety of operators who may be exposed to harmful substances such as PFAS chemicals. This has led to new formulations being developed for solvent cleaners. In applications where formulated blends of halogenated solvents have been used very effectively in the past, these are now required by changes in legislation to be phased out of use.
EnviroTech Europe have been supplying vapour degreasing solvent formulations for over 20 years, constantly responding to increasingly stringent regulatory requirements for environmental and safety laws and the need for improved cleaning standards. Our staff and distributors are trained to work with equipment suppliers to advise on the use of vapour degreasing solvents for the most satisfactory outcome.
EnviroTech Europe have developed a new solvent cleaning formulation based on recent research, a replacement for the “old” technology, which has been found to perform just as effectively without the negative environmental, health and safety issues.
High performance precision cleaning solvent with Zero Ozone Depletion Potential (ODP) and very low Global Warming Potential (GWP)
ProSolv 5408e has been developed to provide superior critical cleaning performance for manufacturers of electronic and electrical components. High Solvency (KB Value 98) for removal of organic residues, compatible with organic and synthetic oils and most plastics and metals.
ProSolv 5408e is a high-performance solvent cleaner used for sustainable and future proof vapour degreasing. It has a GWP of less than 1, with a 100 year Integrated Time Horizon (ITH). Soft on the environment and safe for users, it offers improved cleaning at lower costs.
ProSolv 5408e ticks all the boxes and is the perfect profile for a modern vapour degreasing solvent. Exceptionally low surface tension to penetrate micron sized holes and close contact surfaces. Sustainable and secure for the future. Non-carcinogenic, low boiling point, economical with energy with low solvent losses, faster production, reduced costs, easy handling.
ProSolv 5408e is compatible with most solvent cleaning systems including one-tank or multi-tank immersion and vapour degreasing equipment, using ultrasonics or flush cleaning. An excellent choice for removal of a wide range of organic soils by vapour degreaser, ultrasonic cavitation, dip tank, flushing. Energy-efficient, fast processing, low solvent loss, and easy handling, reducing both environmental impact and operating costs.
FEATURES AND BENEFITS
- PFAS Exempt
- GWP of less than 1
- Non-hazardous for transportation.
- Non-flammable (No Flash Point).
- Not classified as a carcinogen.
- RoHS compliant.
- Fast precision cleaning with short cycle times, fast drying.
- Stable with no additives, no testing required.
- Mid-range boiling point (46°C).
- High Solvency (KB Value 98) for a variety of contaminants.
- Compatible with a broad range of substrates.
FURTHER INFORMATION
Please visit our website https://www.envirotech-europe.com/prosolv5408e for information about other uses and applications for ProSolv®5408e.
Visit www.envirotech-europe.com/applications-and-case-studies for information about uses and applications for all EnviroTech Europe products.
For more advice, please telephone us on +44 (0) 20 8281 6370 or use our website contact form. All products are supplied and supported by EnviroTech Europe Ltd. Manufactured in the United Kingdom and available on short delivery times through our dedicated team of distributors worldwide.
Share this page:
Next-generation, PFAS-Free vapour degreasing solvents
Next-generation, PFAS-Free vapour degreasing solvents for modern industry
ProSolv®5408e is a next-generation, PFAS-free solvent that offers zero Ozone Depletion Potential (ODP) and low Global Warming Potential (GWP below 1), future-proofing your cleaning applications. Effectively removes organic residues and oils and is compatible with most plastics and metals. Exceptionally low surface tension and strong solvency allows it to reach tight spaces, blind holes and micron-sized holes.
ProSolv®5408e is compatible with most solvent cleaning systems including one-tank or multi-tank immersion and vapour degreasing equipment, using ultrasonics or flush cleaning. An excellent choice for removal of a wide range of organic soils by vapour degreaser, ultrasonic cavitation, dip tank, flushing. Energy-efficient, fast processing, low solvent loss, and easy handling, reducing both environmental impact and operating costs.
THE SOLVENT OF CHOICE FOR HIGH PERFORMANCE CRITICAL CLEANING
ProSolv®5408e has a unique range of characteristics which make it the vapour degreasing solvent of choice for critical cleaning applications in the following industries:
- Avionics and Aerospace
- Electronics and Electrical
- Environmental
- General Cleaning
- Industrial and Manufacturing
- Marine and Maritime
- Mechanical Engineering
- Medical Device Manufacturing
- Military
- Motorsport
- Oxygen Cleaning
- Precision Optics
- Power Generation
- Railways and Automotive
FEATURES AND BENEFITS
- PFAS Exempt
- GWP of less than 1
- Non-hazardous for transportation.
- Non-flammable (No Flash Point).
- Not classified as a carcinogen.
- RoHS compliant.
- Fast precision cleaning with short cycle times, fast drying.
- Stable with no additives, no testing required.
- Mid-range boiling point (46°C).
- High Solvency (KB Value 98) for a variety of contaminants.
- Compatible with a broad range of substrates.
FURTHER INFORMATION
Please visit our website https://www.envirotech-europe.com/prosolv5408e for information about other uses and applications for ProSolv®5408e.
Visit www.envirotech-europe.com/applications-and-case-studies for information about uses and applications for all EnviroTech Europe products.
For more advice, please telephone us on +44 (0) 20 8281 6370 or use our website contact form. All products are supplied and supported by EnviroTech Europe Ltd. Manufactured in the United Kingdom and available on short delivery times through our dedicated team of distributors worldwide.
Share this page:
Related Posts
Discontinued 3M™ Novec™ Engineered Fluids
DISCONTINUED 3M™ NOVEC™ ENGINEERED FLUIDS – SWITCH SEAMLESSLY TO PROSOLV® DIRECT REPLACEMENTS
In December 2022, 3M™ announced their plans to discontinue their Novec™ range of PFAS substances (per- and polyfluoroalkyl) in its product line. Final order dates were on March 31st 2025 and the supply of these products will end on December 31st 2025.
This affects the following 3M™ product lines:
3M™ Novec™ Engineered Fluids 3M™
Fluorinert™ Electronic Liquids
The phase-out has left many industries, including electronics, aerospace, medical, and precision engineering, scrambling for viable replacements that match the performance characteristics of Novec™ products, and businesses around the world who rely on these solvents for vapour degreasing applications are now seeking reliable alternatives.
EnviroTech Europe offers a range of direct replacements for the discontinued 3M™ Novec™ products, providing companies with a seamless transition without compromising performance, safety, cost, or compliance. Our ProSolv® Direct Replacements have been specifically developed to be exact chemical replacements for all Novec™ fluids. These high-performance solvents are designed to match all the properties and specification of the relevant Novec™ solvent, ensuring an easy transition with minimal process modifications
Benefits of switching to ProSolv® Direct Replacements range
Seamless integration: Compatible with existing vapour degreasing and precision cleaning systems. Superior cleaning performance which effectively removes oils, greases, and particulate contaminants.
Environmentally responsible: Low GWP, non-ozone depleting, REACH-compliant, safe and sustainable, non-flammable and designed for long-term availability.
Support: Our technical staff provide free-of-charge consultation visits and product trials to help guide your transition away from 3M™ Novec™ engineered fluids.
ACT NOW TO SECURE YOUR SUPPLY.
Businesses must act fast to maintain operational efficiency. EnviroTech Europe can provide a full assessment of your current cleaning process to put in a plan to help ensure a seamless transition. We have already successfully transitioned many Novec™ users globally to our ProSolv® Direct Replacements range, ensuring reliability and compliance for years to come.
NEXT GENERATION, PFAS-FREE SOLVENT CLEANING SOLUTIONS.
EnviroTech Europe also supplies ProSolv®5408e, a PFAS-Free high performance vapour degreasing solvent – offering next-generation, multi-purpose solvent cleaning with zero ODP (Ozone Depletion Potential) and near zero GWP (Global Warming Potential). ProSolv®5408e is tested to a number of industry standards including ASTM D3828, ASTM E918, Stock Loss ARP1755B and ASTM F945-1.
FURTHER INFORMATION
Please visit our website www.envirotech-europe.com/replacements-for-3M-Novec-engineered-fluids for more information about replacing 3M™ Novec™ solvents.
Visit www.envirotech-europe.com/prosolv5408e for information about our next-generation PFAS-free vapour degreasing solvent cleaners. For more advice, please telephone us on +44 (0) 20 8281 6370 or use our website contact form.
Share this page:
Related Posts
Co-solvents for electronics cleaning
Co-solvent cleaning enhances the solubility of contaminants and improves efficiency and performance
What is co-solvent cleaning?
Co-solvent cleaning is a powerful and versatile vapour degreasing process that uses a combination of two solvents to clean a variety of substrates. Particularly useful in electronics cleaning, this process is a safe and efficient way to remove organic and mineral residues from solder fluxes and pastes.
The co-solvent cleaning process uses a mixture of the solvating agent (Topklean EL20A) and a rinsing agent (ProSolv®IPA) in the first cleaning stage, followed by just the rinsing agent in the second stage. Excellent for applications where solubility, material compatibility, sustainability and regulatory compliance are important. Perfect for cleaning circuit boards, semiconductors, avionics, and optical instruments. Co-solvents will help to dissolve contaminants that a single solvent alone may struggle to remove by modifying the overall polarity, viscosity, and evaporation rate of the cleaning solution.
High quality and versatile co-solvents from EnviroTech Europe
Topklean EL20A is designed to clean solder paste deposits, fluxes and other residues in the production of PCBs, offering excellent cleaning capacity and a very low environmental impact. Designed for use in a co-solvent process to remove residues and leave the surface free of organic and inorganic deposits.
ProSolv®IPA is an environmentally friendly azeotropic solvent cleaner – Ideal for removing adhesives, buffing compounds, drawing oils, fluxes and pastes, greases, hydraulic oils, lapping compounds, resins, inks, silicone oils, and waxes, ensuring thorough and efficient cleaning.
Non-flammable and stable throughout the refluxing of the system, it is ideal for applications such as light surface contamination cleaning, fingerprint removal, tank flushing, dust particle cleaning (metallic, glass or plastic) and precision rinsing. Use Topklean EL20A in conjunction with ProSolv®IPA to enhance cleaning and drying performance.
The co-solvent cleaning process for electronics cleaning
Increasing demand for miniaturized electronic assemblies has led to greater challenges in the parts cleaning process, and manufacturers need to solder with greater precision to avoid problems like corrosion and short circuiting. Co-solvent cleaning enhances the solubility of contaminants, improves efficiency and performance, and helps remove difficult soils which often require high temperatures. Perfect for cleaning small components, high density PCB’s or boards populated with very low stand-off components.
A Simple 3-Step Process
Cleaning: Parts are immersed in the boiling sump, which contains a blend of Topklean EL20A and ProSolv®IPA. The low viscosity of the mixture allows for the cleaning of small components and high-density PCB’s.
Rinsing: Parts are rinsed in the clean sump of the vapour degreasing tank, which is filled with ProSolv®IPA. With the co-solvent process,
re-deposition of soils is minimized.
Final stage: Components are moved into the vapour zone for drying, without the need for expensive high-temperature ovens. The entire process is done automatically and under a sealed lid. EnviroTech Europe also supplies vapour degreasing equipment like the Solvac S2 which is perfect for co-solvent cleaning.
CO-SOLVENT CLEANER BENEFITS
- Enhanced solubility
- Improved cleaning efficiency
- Reduced toxicity
- Reduced environmental Impact
- Lower VOC emissions
- Controlled evaporation rates
- Material compatibility
- Low energy / cost efficient
- Regulatory compliance
INDUSTRY APPLICATIONS
- Aerospace and avionics
- Electronics
- Medical device cleaning
- Machining
- Automotive parts and engine cleaning
- Paint and coating removal
- Pharmaceutical and laboratory cleaning
FURTHER INFORMATION
Please visit https://www.envirotech-europe.com/vapour-degreasing-solvents/co-solvent-cleaners/ for more information.
For more advice, please telephone us on +44 (0) 20 8281 6370 or use our website contact form. All products are supplied and supported by EnviroTech Europe Ltd. Manufactured in the United Kingdom and available on short delivery times through our dedicated team of distributors worldwide.
Share this page:
Related Posts
EnviroTech Europe | 2025 Brochure
Advanced solutions for solvent cleaning, vapour degreasing, corrosion protection and metal surface cleaning
EnviroTech Europe supply approved vapour degreasing solvents, solvent cleaners and corrosion protection products. We offer a range of formulations tailored to your industry, which are cost effective, energy efficient, safe for operators and the environment.
We are pleased to introduce our range of products in our 2025 products brochure.
FURTHER INFORMATION
Visit www.envirotech-europe.com/applications-and-case-studies for information about uses and applications for all EnviroTech Europe products.
For more advice, please telephone us on +44 (0) 20 8281 6370 or use our website contact form. All products are supplied and supported by EnviroTech Europe Ltd. Manufactured in the United Kingdom and available on short delivery times through our dedicated team of distributors worldwide.
Share this page:
VIDEO: Phase-out of 3M™ Novec™ Engineered Fluids
PHASE-OUT OF 3M™ NOVEC™ CLEANING AND DEGREASING PRODUCTS – A RANGE OF DROP-IN ALTERNATIVES FROM ENVIROTECH EUROPE
In December 2022, 3M™ announced their plans to stop producing per- and polyfluoroalkyl substances (PFAS) in its product line. Final order dates have now been set for March 31st 2025, and the supply of these products will end on December 31st 2025.
This phase-out affects the following 3M™ product lines:
3M™ Novec™ Engineered Fluids 3M™
Fluorinert™ Electronic Liquids
With 3M™ discontinuing these products, many companies are now evaluating alternatives to find suitable replacements. It’s essential to consider key factors to ensure the replacement not only meets your immediate requirements but also supports long-term success.
Are you affected by the phase-out of 3M™ Novec™ engineered fluids?
At EnviroTech Europe we can offer drop-in replacements for all 3M™ Novec™ cleaning and degreasing products. We understand the uniqueness of every precision cleaning application and provide free on-site visits, technical support and cleaning trials when required. We can provide a full assessment of your current precision cleaning process to put in a plan to help ensure a seamless transition. We have already successfully transitioned many Novec™ users globally to our ProSolv® Direct Replacements range.
Future-proof your solvent cleaning applications with PFAS-Free chemistries.
EnviroTech Europe Ltd also supply future-proof technologies like ProSolv®5408e PFAS-Free high performance vapour degreasing solvent – offering next-generation, multi-purpose solvent cleaning with zero ODP (Ozone Depletion Potential) and near zero GWP (Global Warming Potential), tested to a number of industry standards including ASTM D3828, ASTM E918, Stock Loss ARP1755B and ASTM F945-1.
Act now before 3M™ Novec™ grades become unavailable.
EnviroTech Europe recommends that customers start the transition from 3M™ Novec™ as soon as possible to avoid any potential disruption to your supply chain. Our technical staff can advise on legislative changes to ensure your solvent cleaning solutions stay within regulatory boundaries. We can also provide free of charge consultation visits and free-of-charge product trials to help guide your transition away from 3M™ Novec™ engineered fluids.
FURTHER INFORMATION
Please visit https://www.envirotech-europe.com/vapour-degreasing-solvents/replace-3m-novec-engineered-fluids/ for more information.
For more advice, please telephone us on +44 (0) 20 8281 6370 or use our website contact form. All products are supplied and supported by EnviroTech Europe Ltd. Manufactured in the United Kingdom and available on short delivery times through our dedicated team of distributors worldwide.
Share this page:
Related Posts
Satellite Corrosion Protection
How corrosion protection is being used in the space and satellite industry
Corrosion protection in the space and satellite industry is crucial to prevent degradation of materials in extreme environments. Spacecraft and satellites encounter extremely challenging conditions, such as intense radiation, atomic oxygen, and rapid thermal cycling, all of which accelerate corrosion and material degradation. Effective corrosion protection ensures structural integrity, longevity, and functionality of components, instrumentation and other space infrastructure.
Space and satellite industry structures are designed to operate in highly aggressive and unforgiving environments, where even minor degradation can lead to mission failure or loss of functionality. Corrosion can weaken structural components, making them vulnerable to fractures, cracking, and complete structural failure over time. Satellites and spacecraft also carry vital electronic communication, navigation, imaging, and research equipment. Electronic Corrosion can lead to the failure of critical systems, such as antennas, sensors, solar panels, and propulsion units. Corrosion increases the chance of component fragmentation, leading to debris that contributes to the growing problem of space junk. Without robust corrosion protection, materials might degrade prematurely, shortening the lifespan of the equipment.
With proper corrosion protection, satellite components are less likely to deteriorate, lose functionality or break off, thereby reducing the risk of creating additional space debris and supporting sustainability in orbit. Corrosion-resistant materials and protective coatings like Super CORR A help protect metal and electronic equipment against corrosion and help to minimize the risk of degradation, lowering the frequency and cost of maintenance. Corrosion protection is fundamental to space industry operations, preserving both the physical integrity of the space-based structures and the success of the missions they enable. This is especially vital as the industry moves toward more ambitious projects.
Advanced corrosion protection for the space and satellite industries
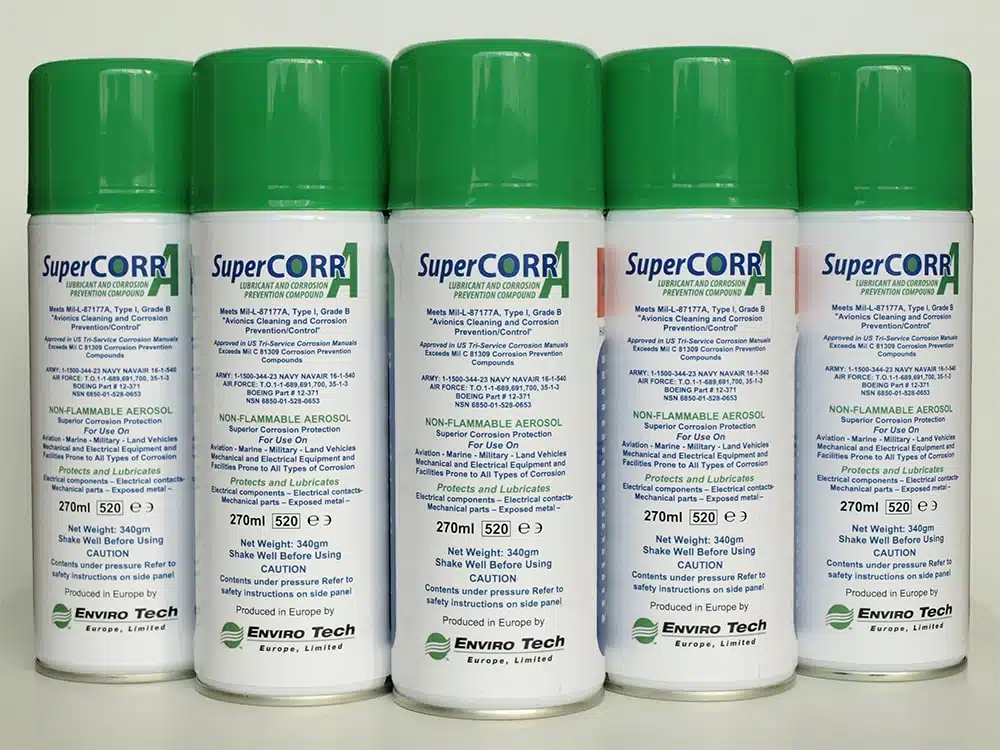
Super CORR A is a unique and proprietary formulation with long-lasting, anti-corrosion inhibitors providing a superior lubrication coefficient and protection against moisture, wear, general and fretting corrosion, static electricity, corona, and other electro migration problems. The non-flammable film is only 7 microns (0.007mm) in thickness, is not a wax or oil-based product and is formulated without sulphates, chlorides, petroleum-based material, or halogens, to meet the EU RoHS directive.
The use of Super CORR A for corrosion prevention can not only bring financial savings in reduced maintenance and replacement costs but more importantly greater safety. It is very effective at preventing corrosion of electronic and electrical equipment in demanding environments.
Super CORR A is a “self-healing” ultra-thin film lubricant with a proprietary corrosion preventive compound that will not harden or crack, is not a wax or oil-based product and is formulated without sulphates, chlorides or halogens.
Super CORR A is packaged in aerosol cans making application to component parts easy for engineering crews in difficult locations and conditions.
EFFICIENT AND ECONOMICAL
- Extremely long-lasting, specially formulated and proprietary anti-corrosive inhibitor.
- Eliminates premature failure of components created by moisture, general or fretting corrosion.
- Prevents deterioration and contamination on all surfaces of electronic and electrical equipment and mechanical close tolerance moving components.
- Reliability increased, maintenance intervals increased and costs reduced, manufacturers save costly warranty service calls or product re-call.
- Non-flammable.
FURTHER INFORMATION
Please visit our website https://www.envirotech-europe.com/supercorr-a for information about other uses and applications for Super CORR A.
Visit www.envirotech-europe.com/applications-and-case-studies for information about uses and applications for all EnviroTech Europe products.
For more advice, please telephone us on +44 (0) 20 8281 6370 or use our website contact form. All products are supplied and supported by EnviroTech Europe Ltd. Manufactured in the United Kingdom and available on short delivery times through our dedicated team of distributors worldwide.
Share this page: