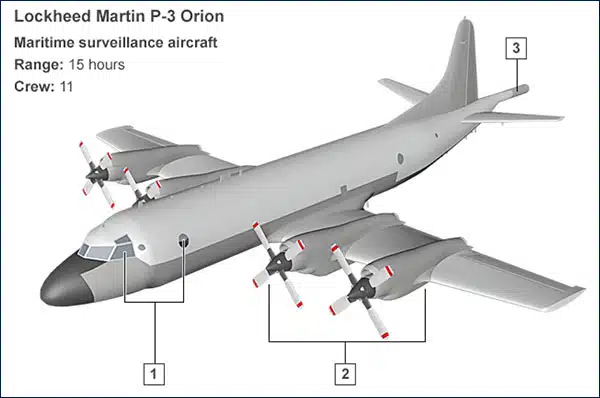
ABOVE:
1. The Lockheed Martin P-3 Orion is equipped with radar and infrared sensors as well as observation posts to help detect any debris on the surface of the ocean. It also has three cameras beneath the landing gear capable of zooming in for a closer look.
2. The four-engine turboprop plane is designed to fly low and slow to aid surveillance. Once it has reached the search location, one or two outer engines can be turned off to preserve fuel and extend the surveillance time.
3. The plane is also fitted with a magnetic anomaly detector (MAD) – used for detecting submarines underwater. The aircraft also has acoustic detectors, which are able to detect sound 1,000ft (304.8m) below the surface of the ocean.
SuperCORR A lubricant keeps Flight MH370 search planes flying
SuperCORR A the lubricant and anti-corrosion formulation from the CORR-EX division of EnviroTech Surface Technologies is helping in the search for the missing Malaysia Airlines flight MH370 passenger jet.
Lockheed Martin AP-3C Orion’s aircraft of the Royal Australian, Korean and Japanese Air Forces used for anti-submarine and maritime surveillance are still searching for debris in a vast area of ocean, bigger than the land area of Europe, southwest of Perth. The maintenance schedules specify SuperCORR A to lubricate and protect the flap tracks and screw jacks in the wings of the aircraft.
SuperCORR A lubricant and protective coating is widely used by the military, electronics and aerospace industries for critical applications to give the protection needed in extreme conditions. SuperCORR Adeposits a dry protective film with excellent corrosion protection and lubricant properties plus the added advantage of a hydrophobic surface rejecting water that ensures the easiest and best connections for very close spaced connectors, contacts, wiring and moving parts.
The U.S. Navy selected SuperCORR A after exhaustive testing using American Society for Testing and Materials (ASTM) Standard B117- Standard Practice for Operating Salt Spray Apparatus. SuperCORR A, a Type I, Grade B Corrosion Preventative lubricant out-performed 11 other products in comparative testing to identify a better product to protect and lubricate the flap tracks and screw jacks on the aircraft.
The flap tracks, located in the aircrafts wings, are what the flaps slide on when they move up or down to lower or increase speed. The screw jacks engage and retract the wing flaps. Corrosion on any of the surfaces can lead to snatching or vibration which can affect the pilots control.
Due to constant operation in salty and corrosive atmospheres which need post-flight rinses and monthly washing down of the aircraft re-lubrication and corrosion treatment for the flap tracks and screw jacks is required each time, with conventional lubricants, to prevent rusting. SuperCORR A was evaluated against competitive products under the Federal Test Method Standard #791B, using a five percent Salt Spray Corrosion Test.
SuperCORR A far exceeded the other products evaluated. After over 200 hours of continuous exposure to salt spray corrosion, SuperCORR A’s protection actually increased over time where the other similar products failed early or contributed to an increase in corrosion.
The accelerated salt fog corrosion testing demonstrated that the application of SuperCORR A which complies with MIL-L-87177A also increased electrical operation to 1400 hours versus 100 hours for the control product used at that time. Technical manuals were updated to include the application for electrical and mechanical parts for civilian and military operations.
The most important conclusion from the historical data and prototype testing is the availability of this excellent corrosion preventive compound that has dry film lubricant properties. The application of SuperCORR A on aircraft components can reduce maintenance man hours, reduce part replacement costs, increase life of aircraft, increase safety, and increase readiness.
Estimates for the maintenance cost for the US Air Force F-16 fleet can reach $500 million per year, the use at all military branches could reach billions of dollars per year. Applications at locations tested by the U.S. Air Force are not normally treated with corrosion prevention and control lubricants (CPC’s) These are the electrical connectors that are susceptible to subtle and not so subtle forms of corrosion that could interfere with the electrical operation of the F-16.
Testing by the U.S. Navy at NADEP Jacksonville incorporates not only electrical connectors, but mechanical and structural components as well. Future uses will also include ground support equipment. The properties of SuperCORR A are such that it can be used on a wide variety of applications and any materials, metal or plastic. Properties of the SuperCORR A far exceed the requirements defined by the MIL-L-87177A specification. Many beneficial properties of the product are not required in the MIL specification.
We can provide you with a Material Safety Data Sheets, independent laboratory reports, product samples and technical assistance.
For more information or advice please telephone us on +44 (0) 20 8281 6370 or use our contact form.
All products are supplied and supported by EnviroTech Europe Ltd. Manufactured in the United Kingdom and available on short delivery times through our dedicated team of distributors worldwide.
Share this page: