Latest Articles
The importance of corrosion protection for avionic and electronic components
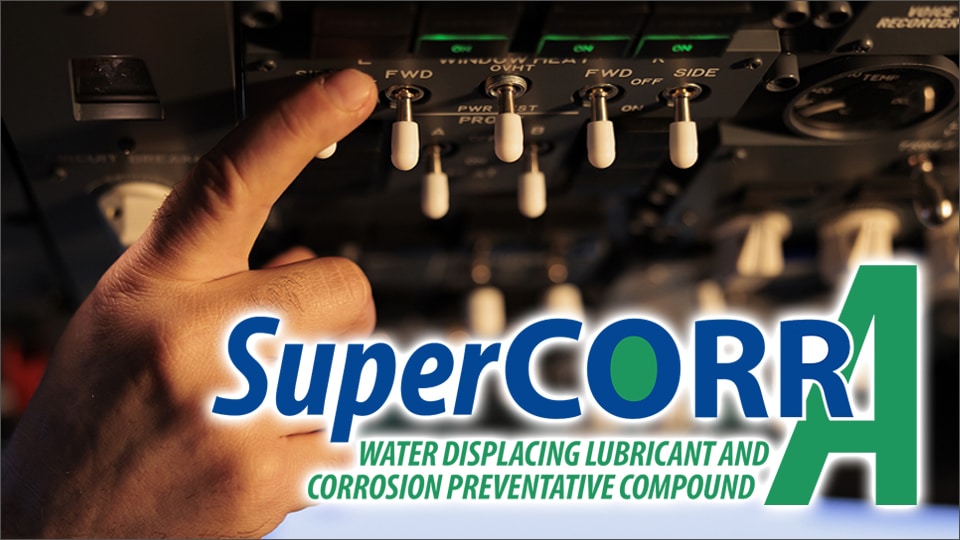
The importance of corrosion protection for avionic and electronic components
Corrosion protection for avionic and electronic components involves a combination of design and maintenance considerations and practices. Environmental testing helps to assess the performance of components under various conditions, including temperature extremes, vibration, humidity, chemical contaminants, moisture and salt exposure. Regular inspection can detect any signs of corrosion, allowing preventive maintenance, cleaning, and application of protective coatings. Corrosion protection is crucial for avionic and electronic components for several reasons:
Reliability and Performance:
Avionic and electronic components are critical for the reliable operation of aircraft and other electronic systems. Corrosion can compromise the functionality of these components, leading to malfunctions, errors, and, in extreme cases, complete failure. Corrosion protection measures help ensure the reliability and optimal performance of these systems.
Safety:
In aviation, safety is paramount. Corrosion can weaken structural components, compromise electrical connections, and interfere with the proper functioning of sensors and control systems. Protecting avionic and electronic components from corrosion is essential to maintain the structural integrity and safety of aircraft.
Longevity and Cost Efficiency:
Avionic and electronic components are often expensive and designed for long-term use. Corrosion can significantly reduce the lifespan of these components, leading to premature failure and the need for costly replacements. Corrosion-related damage can result in expensive repairs and replacements. Implementing effective corrosion protection measures is a cost-effective strategy in the long run, as it helps prevent the need for frequent maintenance and replacements.
Harsh Environmental Conditions:
Aircraft electronic systems are exposed to a variety of harsh environmental conditions, including moisture, salt spray, temperature extremes, and chemical contaminants. These conditions can accelerate corrosion processes.
Maintaining Electrical Connections:
Corrosion on electrical connectors can lead to increased resistance, poor conductivity, and signal degradation. This can affect the accuracy and reliability of data transmission in electronic systems.
Regulatory Compliance:
Aviation and electronic industries are subject to stringent regulations and standards. Many regulatory bodies, such as the Federal Aviation Administration (FAA) in the United States, have specific requirements for corrosion prevention and control. Adhering to these regulations is crucial for ensuring the airworthiness and safety of aircraft.
In summary, corrosion protection for avionic and electronic components is essential for ensuring the reliability, safety, and longevity of critical systems and components. It is a proactive approach to mitigate the damaging effects of corrosion and maintain optimal performance in demanding environments. By incorporating a corrosion protection strategy into the maintenance processes, it is possible to enhance the corrosion resistance of avionic and electronic components, ensuring their reliability and longevity in challenging environments.
SuperCORR A Specialist Barrier Film Corrosion Protection
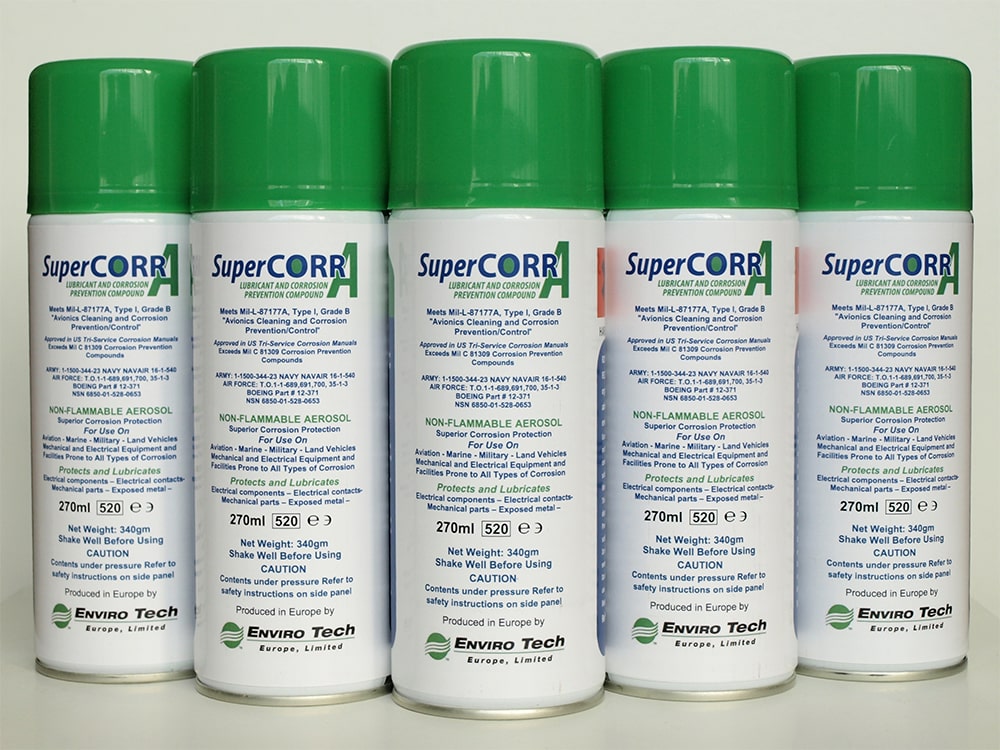
EnviroTech Europe supplies advanced corrosion protection products, based on approved synthetic materials, to provide quality solutions to a diverse range of lubrication and corrosion problems. Super CORR A is a unique and proprietary formulation with long-lasting, anti-corrosion inhibitors providing a superior lubrication coefficient and protection against moisture, wear, general and fretting corrosion, static electricity, corona, and other electro migration problems. The non-flammable film is only 7 microns (0.007mm) in thickness, is not a wax or oil-based product and is formulated without sulphates, chlorides, petroleum-based material, or halogens, to meet the EU RoHS directive.
Super CORR A is unexcelled in preventing failures of electrical systems and electronic equipment caused by corrosion as well as preventing the corrosion of metal components surfaces, including those of components comprised of dissimilar metals such as those found in aerospace environments.The ability to displace water from exposed contacts can ensure reliable operation in extreme conditions. The use of SuperCORR A for corrosion control can not only bring financial savings in reduced maintenance and replacement costs but more importantly greater safety. It is much simpler and a lot less costly to prevent corrosion than to repair or replace damaged avionic equipment or a component that failed because of corrosion.
Super CORR A is packaged in aerosol cans making access to component parts easy for engineering crews in difficult locations and conditions. Unpainted mild steel will not rust on exterior surfaces directly exposed to sea water environments for at least 6 months, protecting electrical connectors, switches, chains, drive shafts from corrosion while maintaining lubrication on moving surfaces.
EFFICIENT AND ECONOMICAL
- Extremely long-lasting, specially formulated and proprietary anti-corrosive inhibitor.
- Eliminates premature failure of components created by moisture, general or fretting corrosion.
- Prevents deterioration and contamination on all surfaces of electronic and electrical equipment and mechanical close tolerance moving components.
- Reliability increased, maintenance intervals increased and costs reduced, manufacturers save costly warranty service calls or product re-call.
HISTORY
SuperCORR A was originally developed for the U.S. Air Force to comply with military specifications and to prevent electrical and electronic components from systems failures caused by corrosion.
It became the industry standard for avionic corrosion protection within MROs (maintenance, repair and operations) and OEMs (overhaul and original equipment manufacturers). It’s unique ability to displace water and provide a performance enhancing level of corrosion protection has led to it being used in many other applications and industries worldwide.
FURTHER INFORMATION
Please visit our website https://www.envirotech-europe.com/supercorr-a for for information about other uses and applications for Super CORR A.
Visit www.envirotech-europe.com/applications-and-case-studies for information about uses and applications for all EnviroTech Europe products.
For more advice, please telephone us on +44 (0) 20 8281 6370 or use our website contact form. All products are supplied and supported by EnviroTech Europe Ltd. Manufactured in the United Kingdom and available on short delivery times through our dedicated team of distributors worldwide.
Share this page:
Solvent cleaners in the nuclear power industry
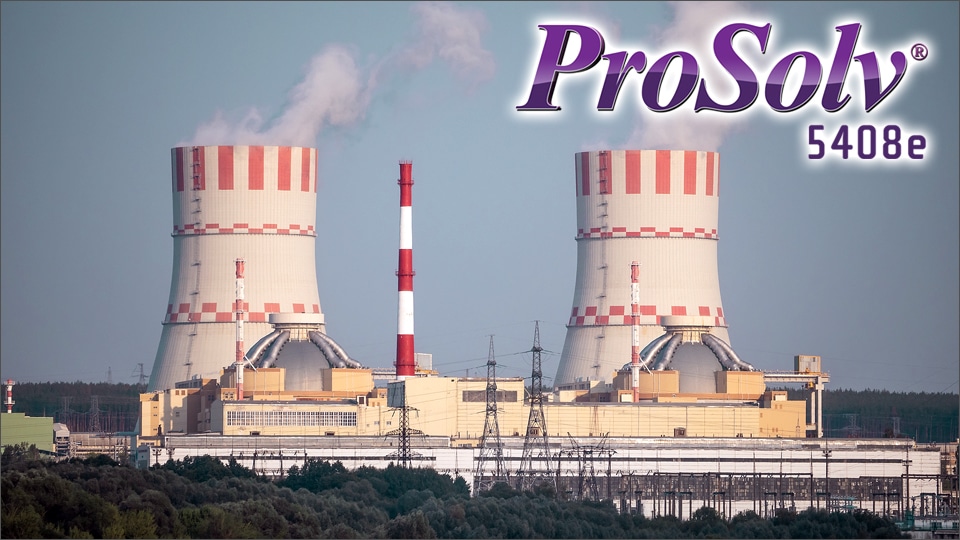
The importance of solvent cleaners in the nuclear power industry
Solvent cleaners play a crucial role in the nuclear power industry for various reasons. The nuclear power industry involves complex and sensitive processes that require a high level of cleanliness to ensure safety, efficiency, compliance with regulatory standards, and overall integrity of nuclear facilities. Here are some key reasons which highlight the importance of solvent cleaning in the nuclear power industry:
Contamination Control:
Nuclear power plants operate in environments where even small amounts of contaminants can have significant consequences. Solvent cleaning helps control and remove contaminants such as dust, dirt, oils, and other foreign residues from various components, ensuring the integrity of critical systems and equipment.
Radiation Protection:
Radioactive materials are present in different forms within nuclear power facilities. Solvent cleaning is essential for decontaminating surfaces exposed to radiation. Radioactive particles can adhere to equipment and structures, posing a risk to workers and the environment. Regular solvent cleaning helps mitigate radiation exposure by removing these contaminants and is crucial for minimizing radiation exposure to workers and preventing the spread of radioactive materials.
Equipment Maintenance:
Nuclear power plants rely heavily on sophisticated equipment and control systems for monitoring and managing various processes, including sensors, valves, pumps, heat exchangers, and instrumentation. Solvent cleaning helps maintain the performance and reliability of these components by preventing corrosion and other issues that may arise from the accumulation of contaminants, ensuring accurate and reliable operation.
Preventing Corrosion:
Corrosion can compromise the structural integrity of materials, especially in the presence of radiation and harsh environmental conditions. Solvent cleaning helps remove corrosive agents, protecting equipment and structures from degradation. This helps extend the lifespan of materials and reduces the risk of structural failure.
Quality Assurance and Regulatory Compliance:
The nuclear industry operates under strict quality assurance and regulatory standards. Solvent cleaning is an essential part of maintaining these standards by ensuring that equipment and surfaces meet cleanliness requirements and do not introduce uncertainties or errors into the nuclear processes.
Heat Transfer Efficiency:
In nuclear power plants, efficient heat transfer is essential for optimal performance. The presence of contaminants on heat exchanger surfaces can reduce heat transfer efficiency, leading to decreased performance and potential overheating. Solvent cleaning helps maintain clean surfaces, ensuring effective heat transfer and preventing overheating of components. Some solvents can also be extremely effective as heat transfer liquids.
Preventative Maintenance:
Solvent cleaning is often a part of routine preventative maintenance programs in nuclear facilities. Clean and well-maintained equipment is less likely to experience malfunctions. Regular cleaning helps identify and address potential issues before they escalate, contributing to the overall safety and reliability of the nuclear plant.
In summary, solvent cleaning is integral to the overall safety, efficiency, and longevity of equipment and structures within the nuclear power industry. It plays a key role in helping to control contamination, maintain equipment performance, protect against radiation, help to prevent corrosion and ensure overall equipment reliability. It’s important to note that while solvents are effective cleaning agents, their use should be handled with care. Some solvents can be toxic, flammable, or harmful to human health and the environment, so proper precautions and guidelines should be followed when using them. Additionally, choosing the right solvent for a specific cleaning task is crucial to achieve optimal results without causing damage to the surfaces being cleaned.
Zero Ozone Depletion Potential (ODP) and very low Global Warming Potential (GWP) solvent cleaner for high performance degreasing.
ProSolv® 5408e has been developed to provide superior critical cleaning performance, suitable for many different industries. High Solvency (KB Value 98) for removal of organic residue and oils.
ProSolv® 5408e is a high-performance solvent cleaner used for sustainable and future proof degreasing. It has a GWP of less than 1, with a 100-year Integrated Time Horizon (ITH). Soft on the environment and safe for users, it offers improved cleaning at lower costs.
ProSolv® 5408e ticks all the boxes and is the perfect profile for a modern degreasing solvent. Exceptionally low surface tension to penetrate micron sized holes and close contact surfaces. Sustainable and secure for the future. Non-carcinogenic, low boiling point, economical with energy with low solvent losses, faster production, reduced costs, easy handling.
EFFICIENT AND ECONOMICAL
- Fast precision cleaning with short cycle times.
- Can be used in any vapour degreasing equipment, lower energy consumption and lower maintenance.
- Ideal replacement for Trichloroethylene, n-Propyl Bromide, Perchloroethylene and HCFC based solvents.
- Stable with no additives, no testing required.
- Improved productivity, parts exit the machine cool, dry and spot-free with no drying required.
- Minimal non-volatile residue (>10ppm).
- High density solution, excellent for ultrasonic cleaning.
- Mid-range boiling point (46°C).
- Very low surface tension for penetration into the micron level crevices and holes, efficient cleaning in tight to reach places and complex geometries.
- Easy process monitoring with minimal effort and minimal waste generation, easy reclamation for reuse.
- High Solvency (KB Value 98) for a variety of contaminants.
- Compatible with a broad range of substrates.
SAFE FOR USERS AND THE ENVIRONMENT
- Safe for the environment, Zero Ozone Depletion Potential (ODP).
- Very low Global Warming Potential (GWP)
- GWP of less than 1, AR4 100yr Integrated Time Horizon (ITH).
- Non-hazardous for transportation.
- Non-flammable (No Flash Point).
- Not classified as a carcinogen
Listed above are some of the benefits from using ProSolv® 5408e, a sustainable degreasing solvent for precision cleaning and an economical and efficient replacement solution for cleaning systems using older legacy solvents, which are now either banned or being phased out. EnviroTech Europe have many years of experience and our experts are available to guide you through your solvent cleaner changeover procedures or to advise on equipment.
FURTHER INFORMATION
Please visit our website https://www.envirotech-europe.com/prosolv5408e for information about other uses and applications for ProSolv® 5408e.
Visit www.envirotech-europe.com/applications-and-case-studies for information about uses and applications for all EnviroTech Europe products.
For more advice, please telephone us on +44 (0) 20 8281 6370 or use our website contact form. All products are supplied and supported by EnviroTech Europe Ltd. Manufactured in the United Kingdom and available on short delivery times through our dedicated team of distributors worldwide.
Share this page:
Related Posts
The importance of corrosion protection for air conditioning units
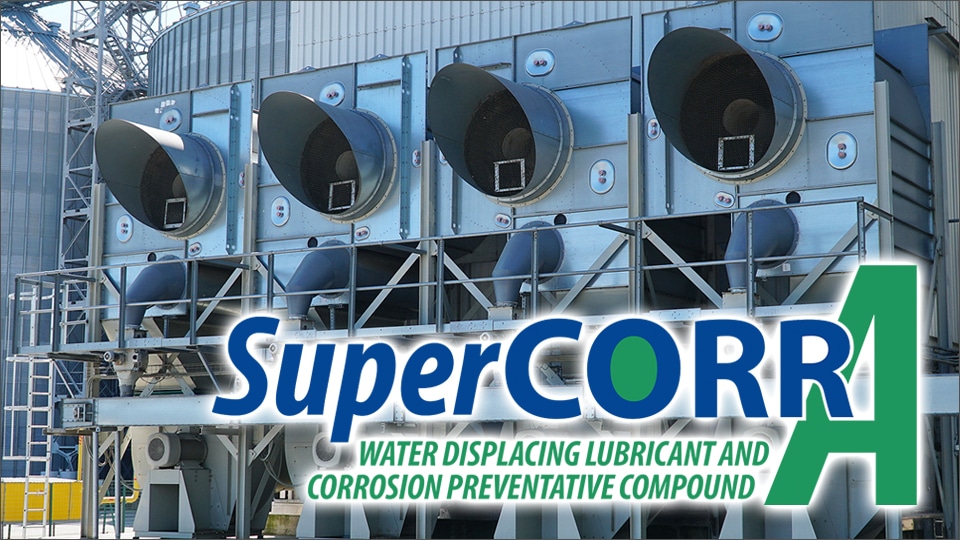
Corrosion protection for air conditioning units.
Corrosion problems in air conditioning units can be caused by various factors including exposure to harsh environmental conditions like humidity, salt, pollutants, chemicals, and other airborne particles, poor maintenance, manufacturing defects or inferior materials, equipment ageing and general wear. To prevent or minimize corrosion in air conditioning units, regular maintenance, proper installation, timely repairs of leaks, and protection against environmental elements are crucial. This includes routine cleaning, inspections, and addressing any issues promptly to extend the lifespan of the AC unit and ensure its optimal performance. Corrosion protection for air conditioning units can be vital in various situations, here are some important considerations:.
Harsh Environments:
In areas near the coast or where the air is laden with salt, the risk of corrosion is higher due to saltwater exposure. Corrosion protection measures, such as coatings or materials designed to resist corrosion, can help extend the lifespan of the air conditioning unit.
High Humidity Environments:
In regions with high humidity levels, the potential for moisture-related corrosion is increased. Protective coatings and treatments can be beneficial in preventing moisture-induced corrosion.
Industrial and Chemical Exposure:
In industrial locations with exposure to corrosive chemicals, protecting air conditioning units from corrosion is important. Acidic or corrosive fumes can deteriorate the unit’s components over time.
Long-Term Maintenance:
Corrosion protection measures can reduce maintenance costs and downtime by preventing or delaying the onset of corrosion-related problems. This is especially important in commercial and industrial applications where HVAC systems are essential for operations.
Extended Equipment Lifespan:
Proper corrosion protection can contribute to the longevity of the air conditioning unit, saving money on replacement costs.
Common methods of corrosion protection for air conditioning units include:
Coatings:
Applying anti-corrosion coatings or paints to the unit’s components to create a barrier.
Galvanized Steel:
Using galvanized steel for components and frames can provide resistance to rust and corrosion.
Regular Maintenance:
Regular cleaning and maintenance to remove corrosive materials like dirt, debris, and salt deposits.
Placement and Enclosure:
Positioning the air conditioning unit in a way that minimizes exposure to harsh elements, or enclosing it in a protective housing, can be effective.
Use of Corrosion-Resistant Materials:
Investing in air conditioning units made from materials that are inherently resistant to corrosion can be a wise choice for long-term durability.
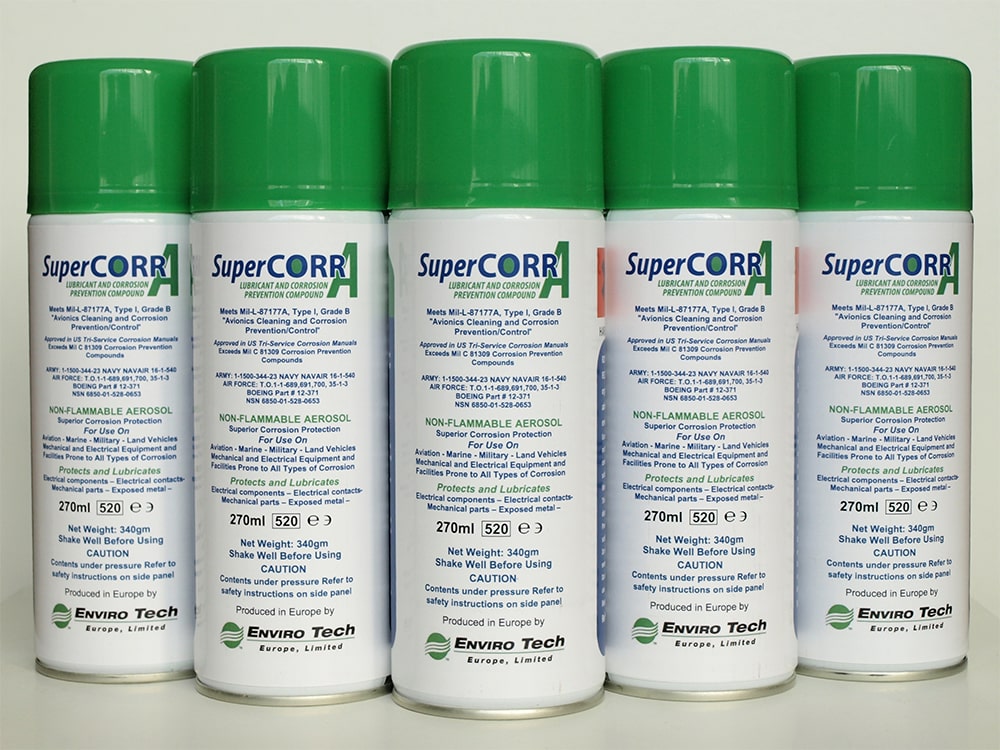
Specialist Barrier Film Corrosion Protection
EnviroTech Europe supplies advanced corrosion protection products, based on approved synthetic materials, to provide quality solutions to a range of lubrication and corrosion problems.
Super CORR A is a unique and proprietary formulation with long-lasting, anti-corrosion inhibitors providing a superior lubrication coefficient and protection against moisture, wear, general and fretting corrosion, static electricity, corona, and other electro migration problems. The non-flammable film is only 7 microns (0.007mm) in thickness, is not a wax or oil-based product and is formulated without sulphates, chlorides, petroleum-based material, or halogens, to meet the EU RoHS directive.
Super CORR A is unexcelled in preventing failures of electrical systems and electronic equipment caused by corrosion as well as preventing the corrosion of metal components surfaces. Use Super CORR A to protect connectors, electrical systems and switches and mechanical controls during servicing. It’s ability to displace water from exposed contacts can ensure reliable operation in extreme conditions, all from one small aerosol can.
The use of Super CORR A for corrosion control can not only bring financial savings in reduced maintenance and replacement costs but more importantly greater safety. It is much simpler and a lot less costly to prevent corrosion than to repair or replace the damaged equipment or component that failed because of corrosion.
Super CORR A is packaged in aerosol cans making access to component parts easy for engineering crews in difficult locations and conditions. Unpainted mild steel will not rust on exterior surfaces directly exposed to sea water environments for at least 6 months, protecting electrical connectors, switches, chains, drive shafts from corrosion while maintaining lubrication on moving surfaces.
EFFICIENT AND ECONOMICAL
- Extremely long-lasting, specially formulated and proprietary anti-corrosive inhibitor.
- Eliminates premature failure of components created by moisture, general or fretting corrosion.
- Prevents deterioration and contamination on all surfaces of electronic and electrical equipment and mechanical close tolerance moving components.
- Reliability increased, maintenance intervals increased and costs reduced, manufacturers save costly warranty service calls or product re-call.
APPROVED
- Industry approval from: NASA, Boeing Aircraft, Bombardier, Embraer, Lear, Gulfstream, Hawker-Beechcraft, Cessna, Raytheon, Polish Airforce, Northrop-Grumman, Royal Navy and Royal Norwegian Air Force.
- Exceeds Mil C 81309 Corrosion Prevention Compounds.
- Approved in US Tri-Service Corrosion Manuals.
FURTHER INFORMATION
Please visit our website https://www.envirotech-europe.com/supercorr-a for for information about other uses and applications for Super CORR A.
Visit www.envirotech-europe.com/applications-and-case-studies for information about uses and applications for all EnviroTech Europe products.
For more advice, please telephone us on +44 (0) 20 8281 6370 or use our website contact form. All products are supplied and supported by EnviroTech Europe Ltd. Manufactured in the United Kingdom and available on short delivery times through our dedicated team of distributors worldwide.
Share this page:
Latest News
Cleaning solvent for vapour degreasing in the aerospace industries
ProSolv® 5408 sustainable, economical cleaning solvent for vapour degreasing in the aerospace industries
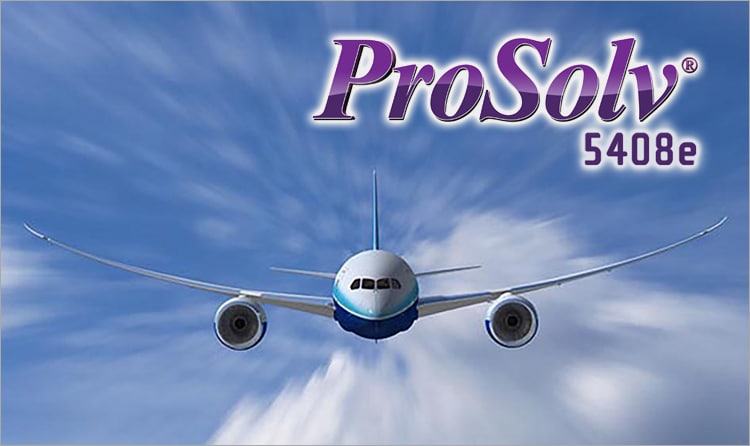
The aircraft and aerospace component manufacturing industries face many critical cleaning applications during manufacturing processes and for finishing where surfaces need to be completely degreased leaving no residues. Although aqueous cleaning would seem to be the method of choice for environmental reasons with new advancements in cleaning solvent chemistry this is often not the case. Vapour degreasing is the most effective process, economical in use with lower energy uses, one tank needing less floor space than multi tank water-based systems and safe for users.
ProSolv 5408e has been developed to be used in place of the traditional chlorinated hydrocarbon solvents, trichloroethylene and perchloroethylene and those based on n-propyl bromide (nPb) which have been phased out for use as vapour degreasing solvents in the EU. The ProSolv 5408e advanced formulation, based on sustainable solvents, has been extensively tested with oils, soils greases and other contaminants from the manufacturing process and with is high KB value all these materials are easily removed to comply with aircraft standards for cleaning and degreasing to the highest levels. No titanium surface cracking or deleterious effects on other metals or composites commonly used for aircraft and aerospace component manufacture have been identified.
The innovative ProSolv 5408e formulation produced by Envirotech Europe ticks all the boxes with the perfect profile for vapour degreasing Soft on the environment with near zero ozone depletion potential (ODP) and very low global warming potential (GWP) its lower boiling point at 48C minimises energy requirements giving reduced process times for greater throughput and comfortably handled critically cleaned parts. The incredibly low surface tension guarantees penetration into micron sized through and blind holes and between close contact surfaces.
Stable in use ProSolv 5408eis safe for users with a high 8hr occupational exposure level of 220ppm. The solvent needs no additives or stabilisers and requires no testing. Sustainable, safe and secure for future use as your forever solvent.
CRITICAL CLEANING FOR THE AIRCRAFT INDUSTRY
A few examples of the many uses are discussed below, our technical service engineers can offer information and advice on critical cleaning in the multitude of other applications experienced in the precision engineering industries.
BONDING OF HONEYCOMB SECTIONS FOR COMPOSITES
An instance of critical cleaning is removal of all contamination from aluminium honeycomb prior to epoxy resin bonding of the formed aluminium skin to produce lightweight high tensile structures for applications such as leading edges on aircraft wings and wind turbine blades. This is an extremely demanding application, as any residues will prevent the adhesion of the adhesives leading to delamination with potentially disastrous effects.
Due to the high standards of cleaning which are required this process is usually carried out by vapour/liquid degreasing with the traditional chlorinated solvents however due to the increasingly stringent controls on these materials ProSolv 5408e which is fully tested to aircraft industry standards and with its greatly improved environmental and user profile is now increasingly used as the sustainable and safer replacement.
CLEANING FOR CRACK AND FAULT TESTING OF WELDS AND CASTINGS
Another common use in the aircraft industry is in the cleaning of castings and metal fabrications before the use of NDT crack detection fluids. Removal of all surface contamination from manufacturing processes is vital to expose faults. Vapour degreasing and vapour liquid cleaning with ultrasonics is a favoured method due to the excellent solubility of oils and greases and other soils using one tank with very fast processing and parts emerging completely clean and dry. Crack and fault detection in casting and welds is also important in other industries such as railways, automotive engines, and turbines where castings or critical welded fabrications are used. This is particularly relevant as part of the maintenance procedure for refurbishment of aircraft landing gear where surfaces can be heavily contaminated by hard to remove hydraulic oils, rubber and cement dust and grease.
Because this application needs completely degreased, residue free and dry surfaces, the use of slow drying cleaners such as hydrocarbons or water-based cleaners may cause problems as the cracks need to be dry to allow penetration of the detection fluids. Vapour degreasing is the most effective cleaning system for all NDT applications as parts emerge dry from the cleaning process. ProSolv 5408e conforms to SaE-AMS2664 and E1417 99-1/7-1-1 solvent precleaning standard for Penetrant testing in aerospace applications.
CRITICAL CLEANING OF OXYGEN AND GAS SYSTEMS
Critical cleaning of oxygen lines and tanks where no organic residues can be tolerated is another ideal use for this new sustainable cleaning solution. ProSolv 5408e conforms to CGA, ELIGA and Compressed Gas Association standards for this application. We have a series of guides to using ProSolv 5408e for component cleaning to Oxygen standards and recommended cleaning methods involved, available on request.
ProSolv 5408e is produced to consistent quality standards worldwide and is available through a network of experienced and qualified suppliers.
For full product information please visit www.vapour-degreasing.com/prosolv5408e
We can provide you with a Material Safety Data Sheets, independent laboratory reports, product samples and technical assistance.
For more information or advice please telephone us on +44 (0) 20 8281 6370 or use our contact form.
All products are supplied and supported by EnviroTech Europe Ltd. Manufactured in the United Kingdom and available on short delivery times through our dedicated team of distributors worldwide.
Share this page:
Related Posts
Corrosion protection for electrical control systems in Wastewater Treatment Plants
SuperCORR A protects electrical control systems against corrosive environments
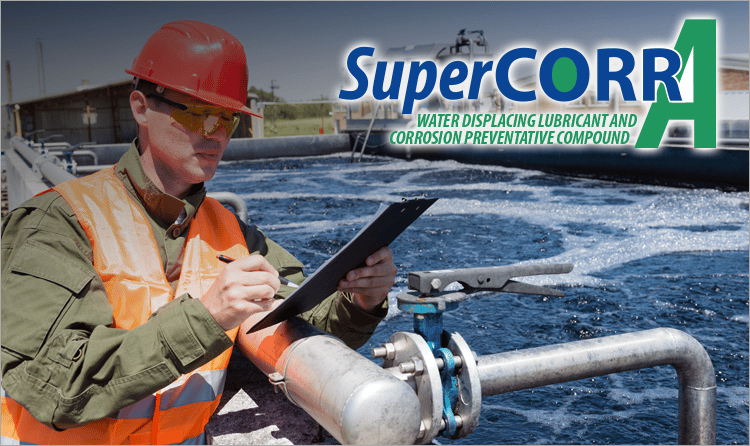
Wastewater treatment plants are subject to corrosion and rust from a variety of causes, one of which is Hydrogen Sulphide gas, (H2S). Corrosion is an insidious and costly problem that causes just about every metal and metal alloy to fail over time. Metals in electrical and electronic control systems, components, connectors, and switches are of most concern.
Corrosion is found in almost all process industries including wastewater treatment plants, pulp and paper mills, fertilizer plants, and numerous other industries and is not going away. Establishing a ‘Preventative Maintenance Program’ that includes corrosion prevention makes it a problem that can be cost effectively dealt with.
One proven and positive way to reduce, if not prevent, corrosion altogether from causing electrical, electronic systems and component failures is by using an ultra-thin film water displacing lubricant material with corrosion inhibiting compound, SuperCORR A has all these properties.
A proprietary formulation packaged in aerosol cans it uses a non-flammable fast drying carrier solvent. The aerosol is supplied with a flexible tube applicator which allows the protective coating to be applied accurately even in difficult to get to components.
Removal of surface contamination from the metallic contact surfaces on switches and circuit breakers is essential to ensure fault free operation. The aerosol uses the unique
SuperCORR A formulation to lift and remove dust and soils from the metal contact surfaces. An inert compound that neither reduces nor increases the electrical conductivity. SuperCORR A also provides long term protection from corrosion and electrical arcing that can lead to shorts and subsequent circuit failures.
Testing SuperCORR A in corrosive environments
SuperCORR A (MIL-DTL-87177B (Revised MIL-L-87177A) Type 1 Grade B lubricant was subjected to extensive and vigorous Mixed Flowing Gas (MFG) testing at Battelle Laboratories under a U.S. Government contract.
Specifications ASTM B827 and ASTM B845 Class III MFG testing protocol were used. This included gases with high corrosion potentials including Hydrogen Sulphide (H2S), Nitrous Oxide(NO2), and Chlorine (Cl2).
ASTM B845 refers to techniques for mixed flowing gas (MFG) tests containing gases that are applied to evaluate devices containing electrical contacts such as slip rings, separable connectors, electromechanical relays or switch contacts. The MFG tests accelerate corrosive degradation processes. Connectors and contacts within closed electronic cabinets may be affected by an environment of different severity than the outside of these cabinets. ASTM B827 outlines procedures for conducting environmental tests involving exposures to controlled quantities of corrosive gas mixtures. Equipment and methods for gas, temperature, and humidity control for tests to be conducted in a reproducible manner are described.
Reproducibility is measured using control coupons whose corrosion films are evaluated by mass gain, coulometry, or by various electron and X-ray beam analysis techniques. Reproducibility can also be measured by in situ corrosion rate monitors using electrical resistance or mass/frequency change methods. Full copies of these tests can be made available on request.
Industrial applications
SuperCORR A has a proven performance record in protecting electrical components, systems, connectors and electronics. The coating will also prevent the ingress of moisture and other contaminants onto the connector surfaces. These initiate corrosions and cause intermittent component failure or a premature degradation of component performance.
The Battelle Laboratories studies provided data and related processing information validating the benefits of using SuperCORR A. to protect the electrical connectors of line replacement units (LRUs) used in military aircraft avionic applications.
The results of the laboratory and field-testing activities conducted in these studies confirm that SuperCORR A is an extremely effective coating to protect electronics, electrical components and systems including switches and connectors with no compromise of the integrity of the electrical component/system even in very corrosive environments.
As a result of testing on site at a number of private and public companies with the confirmatory work at Battelle Laboratories SuperCORR A is being used to reduce maintenance and repair costs in a range of different industrial applications – wastewater treatment plants, pulp and paper mills, automotive and heavy equipment industries and in the power production sector oil and gas and renewable energy and in both the aviation and maritime industries.
FURTHER INFORMATION
Please visit our website www.envirotech-europe.com/supercorr-a for information about other uses and applications. For more advice, please telephone us on +44 (0) 20 8281 6370 or use our website contact form.
All products are supplied and supported by EnviroTech Europe Ltd. Manufactured in the United Kingdom and available on short delivery times through our dedicated team of distributors worldwide.
We can provide you with a Material Safety Data Sheets, independent laboratory reports, product samples and technical assistance.
For more information or advice please telephone us on +44 (0) 20 8281 6370 or use our contact form.
All products are supplied and supported by EnviroTech Europe Ltd. Manufactured in the United Kingdom and available on short delivery times through our dedicated team of distributors worldwide.
Share this page:
Related Posts
Critical cleaning of electronics and electrical components
ProSolv® 5408 new sustainable solvent for critical cleaning of electronics and electrical components
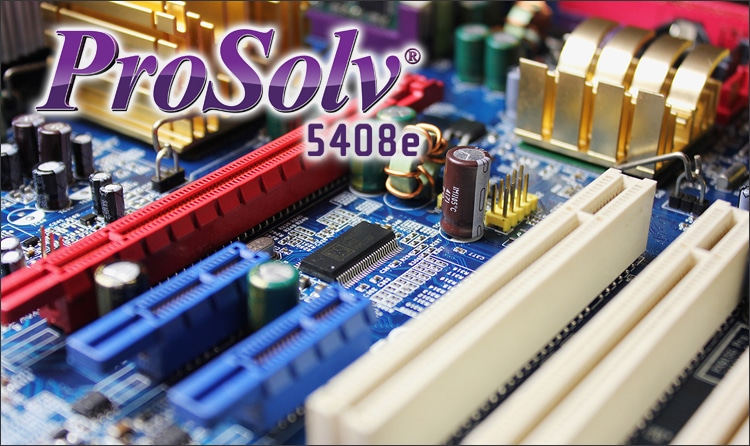
Solvents are used throughout industries where extremely high performance and safety critical cleaning levels are required including aerospace, military and defence, electronics, semiconductor manufacturing, optics, and industrial machining.
ProSolv 5408e is an innovative contemporary highly effective, versatile defluxer developed to not only remove rosin flux, no-clean flux, oil, grease and wax contaminants, but also to eliminate residual halide salts, ions and other polar and non-polar soils and contaminants that often cause component failures with tracking and other issues impacting performance.
Solvents based on conventional chlorinated hydrocarbons have delivered the high standards required for critical cleaning in the past. These chemicals had desirable properties which when combined gave a profile which was perfect for vapour/vapour liquid degreasing when combined with suitable equipment as industrial cleaning systems.
Non-flammable, consistent azeotropes, low viscosity, high liquid density, very low surface tension, and effective wetting enabling them to penetrate tight spaces for optimum cleaning performance. High KB values allows for cleaning a variety of light and heavy soils including particulates, ionic soils, oils, waxes, and greases these are no longer acceptable.
Evolving legislation for ecodevelopment demanded by governments worldwide demand inventive and original formulations for the use of solvents to continue to comply with the increasingly stringent legislation for protection of the environment and, even more importantly, safety of operators who maybe exposed to the products. In applications where formulated blends of halogenated solvents have been used very effectively in the past these are now required by changes in legislation to be phased out of use.
With their 25 years wealth of experience in this field as the inventors of the highly regarded n propyl bromide (nPB) based EnSolv range of precision cleaning solvents EnviroTech Europe created a contemporary new formulation based on recent research and developed a new solvent as a replacement for the “old” technology which has been found to perform just as effectively, but without the negative environmental, health and safety issues.
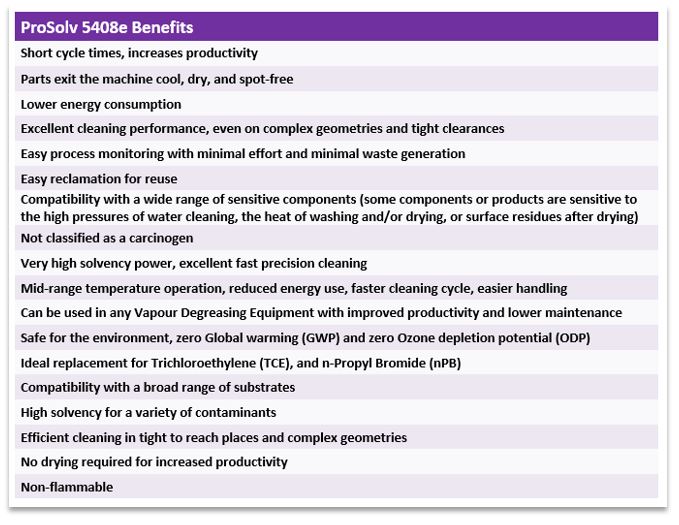
Listed above are just some of the benefits from using ProSolv 5408e, your forever sustainable solvent for cleaning and defluxing in the electronics and electrical components industry and an economical and efficient “drop in “for vapour / vapour liquid cleaning systems using legacy solvents. EnviroTech experts with many years of experience are available to guide you through changeover procedures or to advise on equipment.
For full product information please visit www.vapour-degreasing.com/prosolv5408e
We can provide you with a Material Safety Data Sheets, independent laboratory reports, product samples and technical assistance.
For more information or advice please telephone us on +44 (0) 20 8281 6370 or use our contact form.
All products are supplied and supported by EnviroTech Europe Ltd. Manufactured in the United Kingdom and available on short delivery times through our dedicated team of distributors worldwide.
Share this page:
Related Posts
Medical Device Cleaning
ProSolv® 5408 high performance vapour degreasing solvent for medical device cleaning
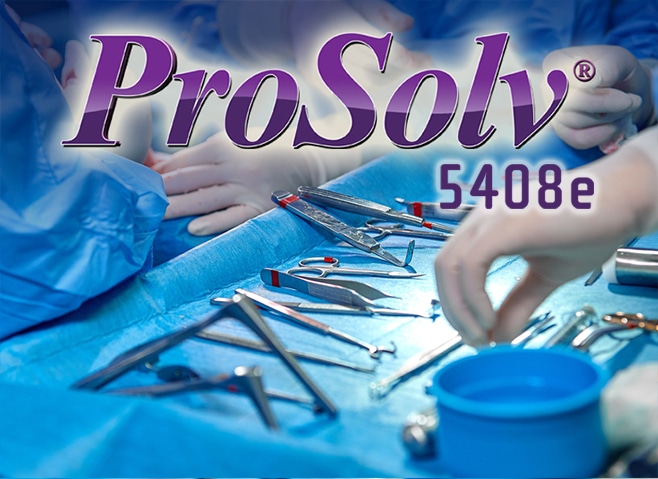
Medical device cleaning
Critical cleaning is vital throughout the medical supply industry for safe, successful operations and procedures. Manufacturers of medical instruments, implants and other devices using metals, glass, ceramics and plastics must select a cleaning processes compatible with all these materials of construction, to remove oils and other contaminants from the manufacturing processes. The cleaning system must be proven to be safety critical and to leave no residues on the surfaces of the cleaned parts.
In this short article we discuss the benefits of condensation cleaning with ProSolv 5408e vapour degreasing solvent for medical device cleaning compared to water-based cleaning.
Water based cleaning options
Formulations for water based cleaners use combinations of surfactants to reduce the very high surface tension of water to allow penetration of the cleaning solution into minutes holes and very fine mechanical clearances. The solutions must solubilise oils, greases, cutting fluids, grinding and buffing compounds and remove particulate soils. Biocides are also present in these formulations to ensure no bioburden is carried over from the cleaning process.
After cleaning residues of chemicals must be removed or they may be a source of corrosion when the devices are in use. Multiple rinses in hot and cold de-ionised water using agitation of baskets or carriers or ultrasound to dilute and displace the cleaning liquids retained in minute holes, cavities and trapped between close tolerance metal surfaces.
Continuous production of high-quality deionised rinse water is extremely expensive, but the drying process is even more costly and environmentally challenging. Multiple cleaning and rinse tanks and drying ovens or tunnels need a lot of space and energy. Further controlled conditions are needed to cool parts after drying to prevent condensation of moisture, which can be growth media for bacteria, on the critically clean surfaces, before packing in sterile bags and containers for storage or shipping.
High output water based cleaning equipment can use conveyorised high pressure targeted spray tunnels for automated high-volume production with integrated “blow off” drying and conditioning tunnels.
For smaller scale operations systems are available using baskets in single cell dishwasher type equipment or open tanks. The latter can use manual or automated handling to progress baskets through the cleaning cycle using similar aqueous based chemical formulations with multiple deionised water rinses and a separate drying oven. These systems can process several baskets or carriers at a time so are only suitable for small batch production. In either case long process times will determine the size and complexity of installations.
Compare the complications of water-based processing to the simplicity and speed of vapour degreasing using ProSolv® 5408e solvents
Vapour degreasing or more properly condensation cleaning, is a proven process where a non-flammable halogenated solvent, safe for people and the environment is heated in the sump of a tank. Boiling solvent produces a dense vapour which is contained by condensation coils around the inner surfaces at the top of the tank. Solvent condensed on the coils is returned to the sump for reuse in a closed cycle.
Parts to be cleaned at ambient temperature are immersed in the vapour which condenses as solvent on the surfaces of the devices or parts in a continuous stream of perfectly clean solvent until the surfaces reaches vapour temperature when condensation ceases. Vapour degreasing uses only one tank with one liquid. Parts are cleaned, rinsed and dry in 3 to 5 minutes with parts hand hot ready for further processing, storage or packing into sterile packs for shipping.
ProSolv 5408e solvents were developed to provide superior critical cleaning performance for manufacturers of medical devices and equipment. The solvent is stable when used for vapour degreasing or cold dip cleaning and compatible with metals, including titanium, ceramics, glass and most plastics used in producing orthopaedic implants, dental, ophthalmic and surgical tools, lenses etc. ProSolv 5408e is a cost effective and sustainable solution to remove polar and non-polar soils and other contaminants and sets the standard for removal of machining and cutting oils, coolants, greases, grinding, buffing and polishing compounds, while leaving no residue.
Vapour degreasing and dip cleaning with ProSolv 5408e is a very effective steriliser of microbial contaminants. Exposing the microorganisms, which have cell walls made up of organic materials including lipids (Fats), to a powerful solvent is a very efficient disruptor of the cell walls. Once compromised the organism’s inner workings lose this protection and the organism dies reducing the bioburden.
ProSolv 5408e is also an excellent solvent carrier for organic or synthetic medical lubricant. This application for coating needles, cannulas and instruments needs consistent quality and evaporation rate to produce, comfortable, pain free insertion for patients.
In many medical applications oxygen and gas supply systems are needed and cleaning at installation and when extensions of pipework and fittings are added is vital for safety. ProSolv 5408e removes oil and organics leaving residue free, dry surfaces to standards approved by gas supply companies, and is compatible with all metals.
Clearly solvent cleaning and vapour degreasing with ProSolv 5408e is a better choice than water cleaning. Faster throughput, lower costs and sustainability to meet the unique challenges in achieving the high standards demanded for medical device manufacturing.
ProSolv 5408e is manufactured in UK with excellent customer service, technical support and training from qualified distributors throughout Europe.
For full product information please visit www.vapour-degreasing.com/prosolv-medical
We can provide you with a Material Safety Data Sheets, independent laboratory reports, product samples and technical assistance.
For more information or advice please telephone us on +44 (0) 20 8281 6370 or use our contact form.
All products are supplied and supported by EnviroTech Europe Ltd. Manufactured in the United Kingdom and available on short delivery times through our dedicated team of distributors worldwide.
Share this page:
Related Posts
SuperCORR A protection for USB contacts
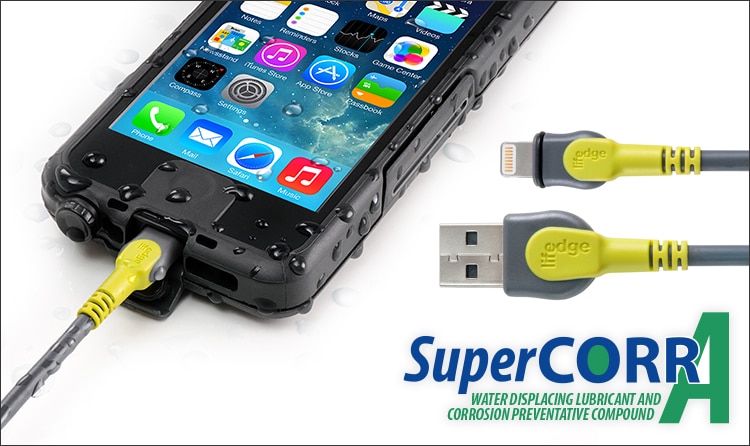
SuperCORR A protects and lubricates contacts on the new Charge / Sync Cable from Lifedge
SuperCORR A lubricant and protective coating widely used by the military, electronics and aerospace industries for critical applications is used to protect contacts on the Lifedge lightning connector to USB cable to offer the protection needed in extreme conditions.
SuperCORR A deposits a dry protective film with excellent corrosion protection and lubricant properties plus the added advantage of a hydrophobic surface rejecting water that ensures the easiest and best connection for the very close spaced connectors.
Lifedge is the world’s first 100% waterproof, rugged Lightning to USB cable for charging and mobile connections whatever the weather or conditions. Developed for use in all outdoor activities including sailing, hiking, military, naval, surveying or other challenging uses. With an ultra-durable outer coating that will never fray and double-moulded, super-tough plugs, charging, downloading and data transfer is improved even in the most extreme and difficult conditions.
During the design of this new cable an extensive test programme, by Scanstrut, manufacturer of the Lifedge cable, was carried out to ensure the contacts were protected from corrosion in the salty and hostile environments in which the Lifedge connectors are used.
SuperCORR A dry lubricant widely used for critical applications in military, electronics and avionics industries proved to offer the protection needed. SuperCORR A prevents or delays corrosion and possible failures.
Testing by a major electronics connector manufacturer recognized that SuperCORR A is a lubricant formulated with corrosion preventive compounds, and as is the case with all “lubricants” will be worn off over time. SuperCORR A was tested to see what the “life” of the lubricant was in a “rub test”. The typical test is 20,000 cycles, i.e. unplug/plug in is one cycle. The test results demonstrated that after 20,000 cycles there were no failures. It was decided to take it one more step and run the same tests for 200,000 cycles. The results again showed no indications of galling or scoring on the USB connectors which looked and performed as good as new.
The extensive testing during the design of the Lifedge connectors validated the original tests and confirmed SuperCORR A will ensure the customer has the most reliable and easy to use connector, in often demanding circumstances. The robust Lightning and USB metal connectors are coated with SuperCORR A patented anticorrosion treatment for complete protection against the elements, whilst an integrated O-ring ensures IP66 waterproofing when charging with the Lifedge iPhone case. The cable is also compatible with protective cases from other leading manufacturers. Officially approved by Apple for use with iPhone, iPad and iPods SuperCORR A helps to bring new freedom and reliability with the Lifedge Ultimate Charge/ Sync Cable.
SuperCORR A is available as an aerosol spray and in bulk containers for brush and dip coating.
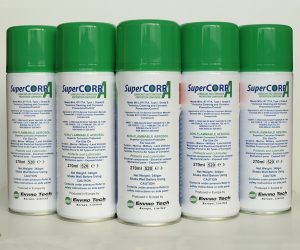
We can provide you with a Material Safety Data Sheets, independent laboratory reports, product samples and technical assistance.
For more information or advice please telephone us on +44 (0) 20 8281 6370 or use our contact form.
All products are supplied and supported by EnviroTech Europe Ltd. Manufactured in the United Kingdom and available on short delivery times through our dedicated team of distributors worldwide.
Share this page:
SuperCORR A Corrosion Protection Spray
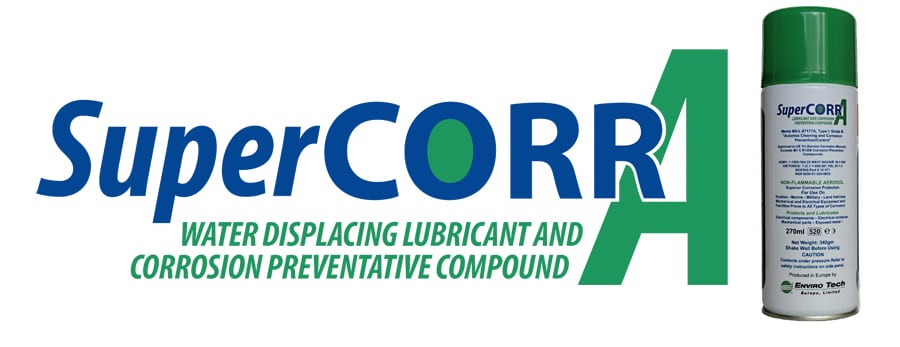
Dry lubricant and corrosion protection spray reduces production downtime on industrial automation systems
Improving manufacturing productivity needs increasing numbers of robots, handling and positioning systems and conveyors which in factory environments need both scheduled and emergency maintenance plans to ensure continuous reliability. Failure of any part of the system will result in downtime and seriously disrupt production.
SuperCORR A from EnviroTech Europe is an innovative thin film dry lubricant spray with corrosion protective properties which does not attract dust or dirt, is stable and coats surfaces with an ultra-thin self healing, lubricant film unaffected by water or solvents and resistant to harsh corrosive atmospheres and high temperatures.
A recent case affected some clients of specialist cleaning equipment manufacturer C&C Hydrosonics a division of U.S giant Crest Ultrasonics to solve a problem occurring on x-y axis linear tracks on the Transystem automatic handling system fitted to enclosed multi tank cleaning systems both aqueous and solvent based.
Transystem automatic handling systems are programmable to automatically process baskets or jigs through liquid immersion cleaning cycles, transferring between the tanks, lowering and raising work between the tanks of cleaning liquids. The motorised carriages use nylon wheels running on case hardened mild steel tracks which can corrode during immersion and in the harsh humid atmospheres within the machine canopies.
Corrosion prevents smooth running with wheels seizing and binding on the tracks. Vibration can then cause components to be shaken from jigs or in extreme cases the carriage will stall requiring intervention by maintenance engineers to physically remove surface corrosion and re-lubricate tracks with oil. This is only a temporary measure as the oil is quickly removed by the solvents or water-based cleaning solutions with corrosion reoccurring in a short time.
Extensive trials over a six-month period with both water and solvent based systems demonstrated that SuperCORR A offered a simple solution to the problem with no corrosion of tracks or seizures during the trial period. Previously seizures needing attention occurred every few weeks now an aerosol spray of SuperCORR A is used only during normal service visits and is used as the routine lubricant during manufacture of the handling system.
Lee Casey, Managing Director of C&C Hydrosonics is delighted with the cost savings on reduced service and maintenance calls using SuperCORR A and that the inconvenience for users of the Transystem equipment has been eliminated. Use of SuperCORR A is recommended on all Crest handling systems worldwide.
Reduce maintenance costs and protect automation equipment with SuperCORR A, now available from EnviroTech Europe Ltd and distributors worldwide.
We can provide you with a Material Safety Data Sheets, independent laboratory reports, product samples and technical assistance.
For more information or advice please telephone us on +44 (0) 20 8281 6370 or use our contact form.
All products are supplied and supported by EnviroTech Europe Ltd. Manufactured in the United Kingdom and available on short delivery times through our dedicated team of distributors worldwide.
Share this page:
Related Posts
Aquus CL-One Concentrated Water Based Cleaner
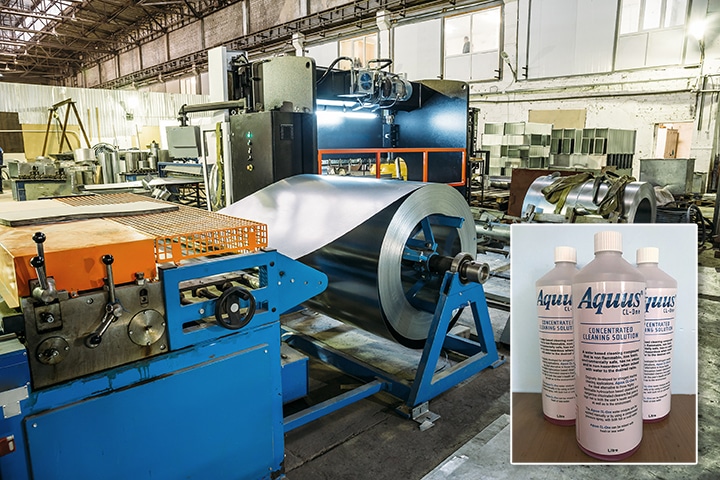
Concentrated water based cleaner for all applications in manufacturing, engineering and general maintenance.
Aquus CL-One cleaner is a new formulation designed to deal with all cleaning applications encountered in manufacturing and engineering. It reduces time and costs by removing the need for multiple cleaning products usually needed to deal with the challenges presented by the wide range of soils, oils and other contaminants which need to be removed. Safe for the environment and users, contains no solvents and is biodegradable within 30 days. Typical applications in industry are discussed below but many more will be experienced in day-to-day operations. With only one product for all cleaning applications incorrect selection or dangerous uses can be avoided.
Concentrated Aquus CL-One chemistry is activated by water, varying concentration levels allows the most economical solution to be chosen for specific applications from parts cleaning to surface preparations for finishing or heavier soiling on process machines all from one product. Some of the hundreds of applications are discussed below.
PARTS AND COMPONENT CLEANING
Ideally suited for cleaning protective coatings, grease and soils from new or used parts. Aquus CL-One can be used in parts washing equipment or dipping tanks without modifications and leaves no residue after drying. Oil and grease separate from the water and coalesces on the surface of the cleaning solution which can then be skimmed off for recovery and recycling. Precipitated solids free of hydrocarbons can be removed by settlement or in filtration systems. The cleaning solution can be reused continuously within its chemical parameters for efficient and economical use.
GENERAL CLEANING
Aquus CL-One is remarkably efficient removing oils, greases, and accompanying dirt from most surfaces. It can be applied by wiping surfaces, mopping or in rotary floor cleaning machines, low or high-pressure spray. Aquus CL-One is also an effective cleaner in industrial kitchens removing grease and baked on deposits on internal surfaces of ovens and trays. For maintenance of machines, engines etc oil and grease is easily removed pre and post-assembly making inspection and repair easier, quicker and cheaper by returning equipment to use.
PREPARATION FOR PAINTING OR POWDER COATING
Aquus CL-One is an excellent choice for cleaning mild steel and ferrous metal parts which are not painted immediately. Process oils and grease on the parts protect the surfaces from changes in humidity but once removed flash rusting can occur while drying. Aquus CL-One prevents this leaving an invisible barrier on the metal surfaces providing extended corrosion protection during storage, fabrication or assembly before finishing. The barrier film can be painted over without additional rinsing and without affecting adhesion of paint or powder coatings. Various cleaning systems can be used, including hand wiping, dip tanks and pressure washing.
Our applications experts and samples of the product are available by completing the contact form at our website. For more information please visit:
Share this page:
Related Posts
Corrosion control problems
Corrosion control is a serious problem for industry and governments worldwide.
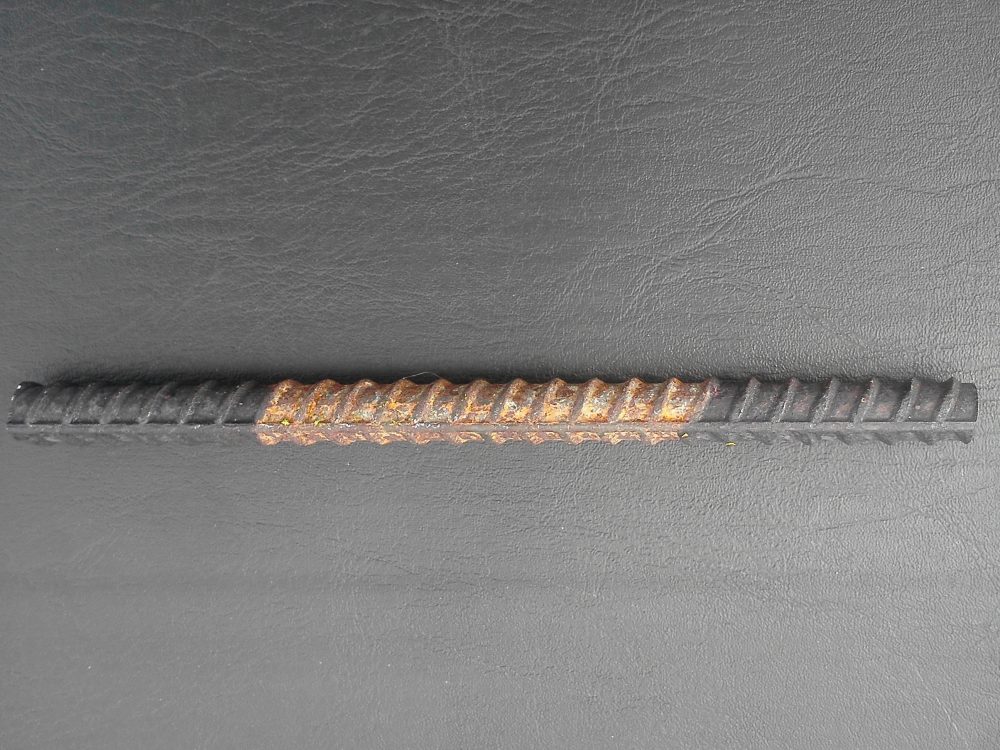
Most people associate corrosion with rust, which only happens in things made of ferrous metals such as steel girders, ships, iron pipes, steel reinforcement rods, and steel tanks and is the reason metals deteriorate and fail.
Ferrous and non-ferrous metals corrode on contact with both fresh and salt water as well as water vapor. They will also corrode when they come in contact with chemicals, liquid acids as well as acidic vapors, salts and bases, and bacteria.
Read our article “Corrosion Control Solutions – A Solution To A Costly Problem” for more information about the enormity of the costs involved in failing to prevent corrosion.
We can provide you with a Material Safety Data Sheets, independent laboratory reports, product samples and technical assistance.
For more information or advice please telephone us on +44 (0) 20 8281 6370 or use our contact form.
All products are supplied and supported by EnviroTech Europe Ltd. Manufactured in the United Kingdom and available on short delivery times through our dedicated team of distributors worldwide.
Share this page: